Forming process of composite material and metal joint
A technology of metal joints and molding process, which is applied to other household appliances, household appliances, household components, etc., can solve the problems of increased weight, stress concentration, and inability to repeatedly disassemble and assemble the connection structure, and achieve the effect of improving rigidity
- Summary
- Abstract
- Description
- Claims
- Application Information
AI Technical Summary
Problems solved by technology
Method used
Image
Examples
Embodiment Construction
[0022] According to the attached figure 1 , 2 The present invention is described further:
[0023] A composite material and metal joint molding process,
[0024] S1. Select the metal joint, and open a plurality of rotary slots arranged side by side along one end of the metal joint. Each rotary slot is a closed circle that rotates along the radial direction, and waves are formed between each rotary slot and adjacent rotary slots. broken line structure;
[0025] S2. Lay the axial unidirectional material along the length direction along the metal joint as a whole,
[0026] S3. After the axial unidirectional material is paved, the prepreg is paved in the direction of the proportional interval ±45°,
[0027] S4. Lay hoop-direction fiber fabric for each gyratory until the height of the layer is equal to the peak of the wavy fold line structure, and complete the laying of the joint position according to the overall force of the co-glued joint and combined with the design principl...
PUM
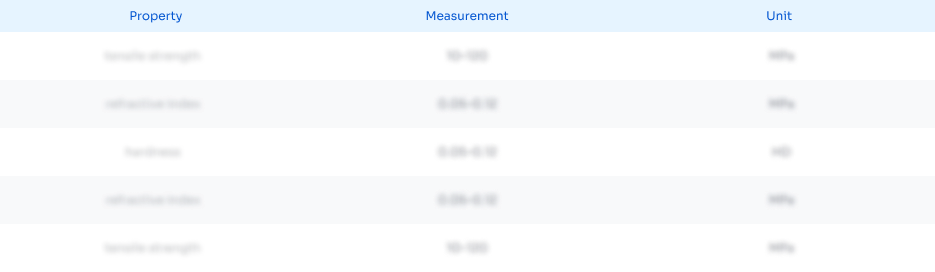
Abstract
Description
Claims
Application Information

- R&D
- Intellectual Property
- Life Sciences
- Materials
- Tech Scout
- Unparalleled Data Quality
- Higher Quality Content
- 60% Fewer Hallucinations
Browse by: Latest US Patents, China's latest patents, Technical Efficacy Thesaurus, Application Domain, Technology Topic, Popular Technical Reports.
© 2025 PatSnap. All rights reserved.Legal|Privacy policy|Modern Slavery Act Transparency Statement|Sitemap|About US| Contact US: help@patsnap.com