Upper shell assembling machine
A technology for assembling machines and casings, applied in the directions of conveyor objects, transportation and packaging, can solve problems such as affecting product quality, dislocation of the circumferential position of the upper casing, affecting production costs and efficiency, and avoiding accidental movement.
- Summary
- Abstract
- Description
- Claims
- Application Information
AI Technical Summary
Problems solved by technology
Method used
Image
Examples
Embodiment 1
[0083] Such as Figure 1 to Figure 28 As shown, the upper casing assembly machine includes a support platform 1 on which an upper casing vibration plate 2, an assembly transfer support frame 3, an assembly correction mounting frame 4, an assembly drive mounting frame 5, and an assembly feeding support frame 6 are installed. , transmission frame 7, error-proof positioning support frame 8, assembly positioning support frame 9 and error-proof driving support frame 10;
[0084] A separation drive device 11 is installed on the assembly transfer support frame 3, and the output end of the separation drive device 11 is connected with a feeding transfer plate 12, and several assembly transfer devices that can communicate with the output end of the upper casing vibration plate 2 are arranged on the feed transfer transfer plate 12. slot 13;
[0085] Assembling and rectifying the mounting frame 4 is rotatably connected with several groups of correcting components corresponding to several...
Embodiment 2
[0113] This embodiment makes the following further limitations on the basis of Embodiment 1: the positioning drive device 40 is installed on the error-proof positioning support frame 8 and the assembly positioning support frame 9, and the output end of the positioning drive device 40 is connected with A jig positioning frame 41 that can move up and down. The jig positioning frame 41 has a jig positioning block 42 located above the error-proof positioning and placing plate 31 or the assembly positioning and placing plate 30 .
[0114] In order to realize the positioning of the revolving jig by the fixture positioning frame, preferably, the fixture positioning frame 41 has a positioning connecting plate 67 connected to the output end of the positioning drive device 40, and the two ends of the positioning connecting plate 67 are connected with a positioning support plate 68 , the top ends of the two positioning support plates 68 are connected with the jig positioning block 42 .
...
Embodiment 3
[0120] This embodiment makes the following further limitations on the basis of Embodiment 1: the correction transmission gear 43 is connected to the correction rotating sleeve 2 of each set of correction components;
[0121] The output end of the correction driving device 23 is connected with a correction transmission rack 44 meshing with the correction transmission gear 43 .
[0122] In this embodiment, for structural optimization, the correction transmission gear 43 should be located below the correction outer positioning member 21 . The correction transmission gear 43 can be sleeved on the correction rotation sleeve 15, and fixed by fastening screws.
[0123] Preferably, in order to observe the cooperation between the correction transmission gear 43 and the correction transmission rack 44 , an observation window 72 may be provided on the assembly correction installation frame 4 . In order to protect the operation of the outer orthosis sleeve 19 , the orthotic installation ...
PUM
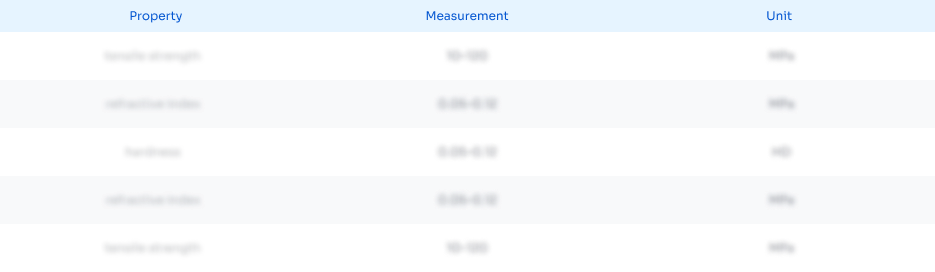
Abstract
Description
Claims
Application Information

- R&D Engineer
- R&D Manager
- IP Professional
- Industry Leading Data Capabilities
- Powerful AI technology
- Patent DNA Extraction
Browse by: Latest US Patents, China's latest patents, Technical Efficacy Thesaurus, Application Domain, Technology Topic, Popular Technical Reports.
© 2024 PatSnap. All rights reserved.Legal|Privacy policy|Modern Slavery Act Transparency Statement|Sitemap|About US| Contact US: help@patsnap.com