Weldless lightweight battery box body and manufacturing process thereof
A lightweight, no-weld technology, applied to battery pack parts, circuits, electrical components, etc., can solve the problems of reduced material performance of side beams, low production efficiency, large product deformation, etc., and it is easy to control the dimensional accuracy, Effects of improving cost and efficiency and reducing equipment cost
- Summary
- Abstract
- Description
- Claims
- Application Information
AI Technical Summary
Problems solved by technology
Method used
Image
Examples
Embodiment Construction
[0061] The following will clearly and completely describe the technical solutions in the embodiments of the present invention. Obviously, the described embodiments are only some of the embodiments of the present invention, rather than all the embodiments. Based on the embodiments of the present invention, all other embodiments obtained by persons of ordinary skill in the art without making creative efforts belong to the protection scope of the present invention.
[0062] see Figure 4 to Figure 18 , the embodiment of the present invention includes:
[0063] A lightweight battery box without welds, comprising: a frame profile, a frame corner 700, a beam 500 and a bottom plate 600, the frame profile is assembled through the frame corner 700 to form a frame group, the beam 500 is installed horizontally inside the frame group and Locked with the left and right sides of the frame group, the bottom plate 600 is buckled on the frame group and locked and fixed with the frame group. ...
PUM
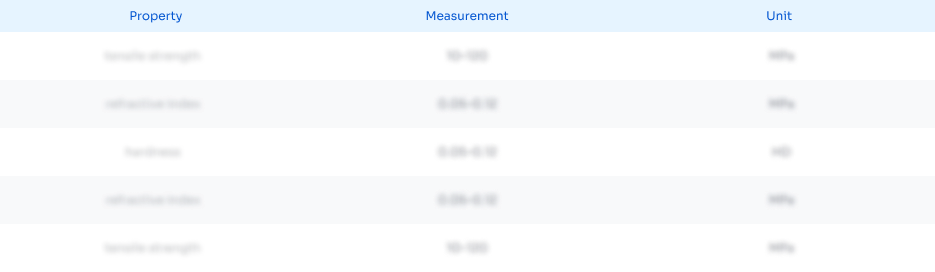
Abstract
Description
Claims
Application Information

- Generate Ideas
- Intellectual Property
- Life Sciences
- Materials
- Tech Scout
- Unparalleled Data Quality
- Higher Quality Content
- 60% Fewer Hallucinations
Browse by: Latest US Patents, China's latest patents, Technical Efficacy Thesaurus, Application Domain, Technology Topic, Popular Technical Reports.
© 2025 PatSnap. All rights reserved.Legal|Privacy policy|Modern Slavery Act Transparency Statement|Sitemap|About US| Contact US: help@patsnap.com