Signal acquisition system for surface acoustic wave magnetic sensor
A signal acquisition system and magnetic sensor technology, applied in the direction of the size/direction of the magnetic field, using magneto-optical equipment for magnetic field measurement, instruments, etc., can solve the problem that small changes in the SAW resonance frequency are difficult to be detected, and the output frequency range of the signal generator Limited, high-frequency SAW devices are difficult to start vibration, etc., to achieve the effect of no test blind zone, simple structure, and high circuit stability
- Summary
- Abstract
- Description
- Claims
- Application Information
AI Technical Summary
Problems solved by technology
Method used
Image
Examples
Embodiment Construction
[0026] The present invention is further described below in conjunction with accompanying drawing:
[0027] like figure 1 As shown, the present invention includes oscillating circuits 1 and 2, a frequency mixing circuit 3, an amplification and shaping circuit 4, and a frequency measurement circuit 5 connected in sequence; the first input end of the frequency mixing circuit 3 is connected to output the oscillation of the SAW sensor measurement frequency signal Circuit 1, the second input end of the frequency mixing circuit 3 is connected to the oscillation circuit 2 outputting the SAW sensor reference frequency signal; the amplification and shaping circuit 4 is connected to the signal output terminal IF of the frequency mixing circuit 3; the frequency measurement circuit 5 is mainly composed of chip STM32F103C8T6, the 16th pin of the chip STM32F103C8T6 is connected to the signal output end of the amplification and shaping circuit 4, the chip STM32F103C8T6 can communicate with th...
PUM
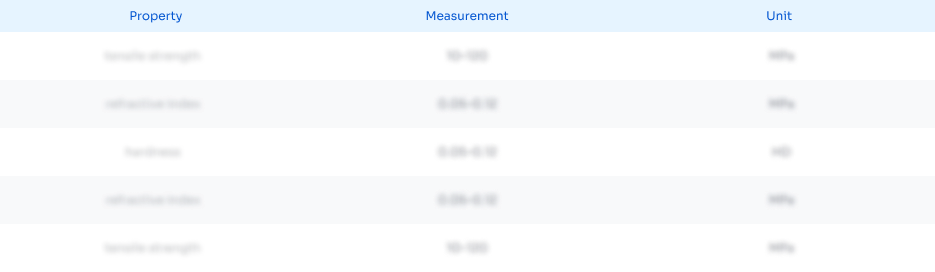
Abstract
Description
Claims
Application Information

- R&D
- Intellectual Property
- Life Sciences
- Materials
- Tech Scout
- Unparalleled Data Quality
- Higher Quality Content
- 60% Fewer Hallucinations
Browse by: Latest US Patents, China's latest patents, Technical Efficacy Thesaurus, Application Domain, Technology Topic, Popular Technical Reports.
© 2025 PatSnap. All rights reserved.Legal|Privacy policy|Modern Slavery Act Transparency Statement|Sitemap|About US| Contact US: help@patsnap.com