Suspension force disturbance control method for self-guided linear propulsion structure for electric repulsion type maglev track
A magnetic levitation track and repulsion-type technology, which is applied in electric traction, electric vehicles, vehicle components, etc., can solve the problems of static power consumption of guiding devices
- Summary
- Abstract
- Description
- Claims
- Application Information
AI Technical Summary
Problems solved by technology
Method used
Image
Examples
Embodiment Construction
[0017] The specific operation method of the present invention will be further described in detail below with reference to the accompanying drawings.
[0018] Refer to the attached figure 1 and figure 2 As shown in the figure, a linear propulsion system with self-guidance proposed in the present invention includes a train body 1, a suspension bogie 2, an independent plate-type electric suspension mechanism 3 installed under the bogie, a supporting guide wheel 4, a hollow core permanent Magnetic linear propulsion system 5, and concrete track 6. The air-core linear propulsion system 5 is composed of an active zero-flux coil chain 8 installed on the track and a Halbach permanent magnet array 7 installed under the center of the vehicle body. Mechanical air gap 9. When the train starts from zero speed, the train is supported by the supporting wheels 4 installed on the suspension bogie; when the running speed of the train reaches the floating speed, the supporting wheels are retr...
PUM
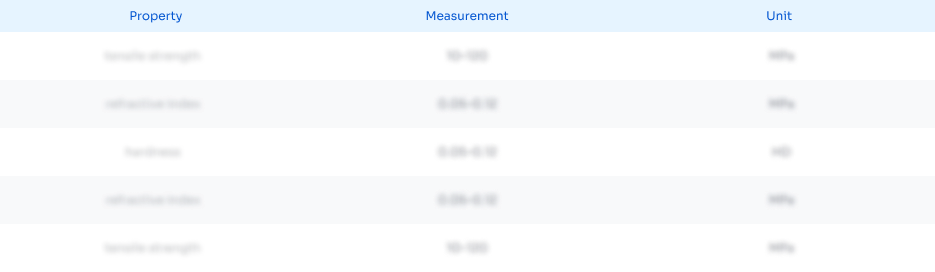
Abstract
Description
Claims
Application Information

- R&D Engineer
- R&D Manager
- IP Professional
- Industry Leading Data Capabilities
- Powerful AI technology
- Patent DNA Extraction
Browse by: Latest US Patents, China's latest patents, Technical Efficacy Thesaurus, Application Domain, Technology Topic, Popular Technical Reports.
© 2024 PatSnap. All rights reserved.Legal|Privacy policy|Modern Slavery Act Transparency Statement|Sitemap|About US| Contact US: help@patsnap.com