Forming method for special-shaped beam with right-angle step
A forming method and step technology, applied in metal rolling and other directions, can solve the problems of inability to process sharp or right-angle structures, inability to realize sharp-angle forming, and long preparation cycle, so as to save raw materials, low cost, and fast forming speed Effect
- Summary
- Abstract
- Description
- Claims
- Application Information
AI Technical Summary
Problems solved by technology
Method used
Image
Examples
Embodiment Construction
[0032] The present invention will be further described below in conjunction with the accompanying drawings and embodiments.
[0033] like Figure 1-6 shown.
[0034] A method for forming special-shaped beams with right-angled steps, with figure 1 The product shown is an example in the Image 6 The final forming on the production line shown includes seven steps of material preparation, cold rolling, heating, hot rolling, cooling, shaping and straightening, specifically including:
[0035] The first step is blanking. According to the size and loss of the final formed product, the steel strip coil is cut into a steel strip coil of the required width; the cutting equipment can be carried out by using the existing uncoiling equipment; The calculation is obtained, and the calculation is performed using the principle of constant volume.
[0036] The second step is to put the cut steel strip on the loading machine at the beginning of the cold rolling production line through the co...
PUM
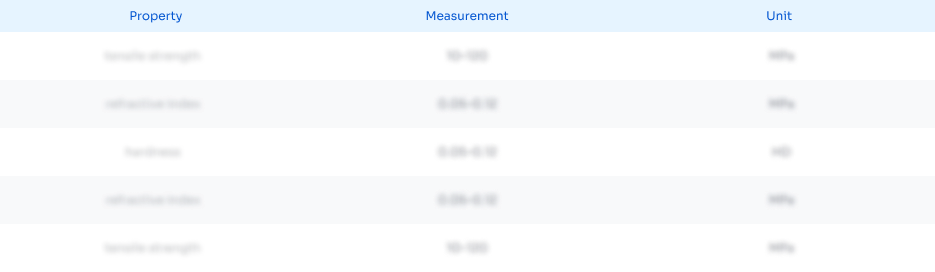
Abstract
Description
Claims
Application Information

- R&D Engineer
- R&D Manager
- IP Professional
- Industry Leading Data Capabilities
- Powerful AI technology
- Patent DNA Extraction
Browse by: Latest US Patents, China's latest patents, Technical Efficacy Thesaurus, Application Domain, Technology Topic, Popular Technical Reports.
© 2024 PatSnap. All rights reserved.Legal|Privacy policy|Modern Slavery Act Transparency Statement|Sitemap|About US| Contact US: help@patsnap.com