Pattern bit blanking die
A jacquard piece and mold technology, applied in the field of knitting machine manufacturing, can solve the problems of increasing mold management cost, no single-tooth mold, and high mold cost, and achieve the effects of high quality, improved precision, and low production cost
- Summary
- Abstract
- Description
- Claims
- Application Information
AI Technical Summary
Problems solved by technology
Method used
Image
Examples
Embodiment 1
[0027] exist figure 1 figure 2 In the shown embodiment 1, a kind of jacquard sheet punching die comprises upper mold base 1, lower mold base 2, punch fixing plate 3 and unloading plate 4, and the center of upper mold base is fixed with an upward protruding Die shank 24, the four corners of lower mold base are provided with parallel upwards protruding and four guide pillars 25 perpendicular to lower mold base, the four corners of upper mold base and guide pillars are correspondingly provided with guide sleeve 26, described guide sleeve and all The guide post forms a sliding pair. The punch fixing plate is a rectangle, and the punch fixing plate is fixed below the upper die seat by the punch backing plate 5, and the punch fixing plate below is correspondingly provided with a die fixing plate 6, and the die fixing plate 6 is fixed. The plate is fixed above the lower die base through the die backing plate 27. The feed side of the punch fixing plate is provided with a horizonta...
Embodiment 2
[0032] exist Figure 5 Figure 6 Figure 7 In the shown embodiment 2, the arrangement direction of the square hole punch is inclined to the feeding direction of the mould, and the rest are the same as in the embodiment 1.
[0033] When the jacquard sheet blanking die of the present invention is produced, the material belt 28 through leveling is sent to the initial position of the mold through the servo feeding system, and the slide block of the punch press drives the entire upper mold to move downward, and the unloading plate first contacts the material belt, and Under the action of the unloading spring, the material belt is pressed to ensure the position of the material belt. The upper die continues to move downward, and the punching punch contacts the material belt to complete the punching action. This punching hole is used for subsequent guidance and misfeed detection. , to ensure that the step distance of the material belt is consistent during the transmission process; f...
PUM
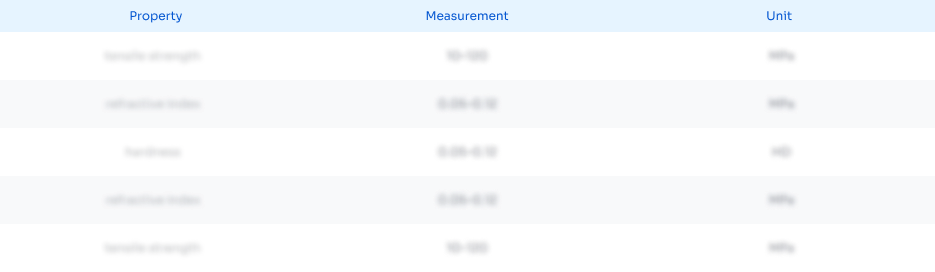
Abstract
Description
Claims
Application Information

- R&D Engineer
- R&D Manager
- IP Professional
- Industry Leading Data Capabilities
- Powerful AI technology
- Patent DNA Extraction
Browse by: Latest US Patents, China's latest patents, Technical Efficacy Thesaurus, Application Domain, Technology Topic, Popular Technical Reports.
© 2024 PatSnap. All rights reserved.Legal|Privacy policy|Modern Slavery Act Transparency Statement|Sitemap|About US| Contact US: help@patsnap.com