Batching system for knitting production
A batching system and knitting technology, applied in thin material handling, conveying filamentous materials, conveyor control devices, etc., can solve the problems of low production efficiency, high labor intensity of workers, easy to make mistakes, etc., to achieve high production efficiency, improve Productivity and the effect of reducing the number of round trips
- Summary
- Abstract
- Description
- Claims
- Application Information
AI Technical Summary
Problems solved by technology
Method used
Image
Examples
Embodiment 1
[0040] Such as Figure 1-Figure 2 As shown, the ingredient system for knitting production provided by this embodiment includes a control module 90, an ingredient conveying line 10, a walking track 20 arranged beside the ingredient conveying line 10, a base 30 arranged on the walking track 20 and a set The manipulator 31 and the material rack 32 on the base 30, wherein the control module is a conventional module, such as a computer, is not the focus of this embodiment, and will not be described in detail here.
[0041] The ingredient conveying line 10 is a roller conveyor that can be purchased directly from the market. It should be noted that the ingredient conveying line 10 may only include one roller conveyor, or may include multiple roller conveyors connected in series sequentially. The actual conveying length needs to be determined. Preferably, in this embodiment, the ingredient conveying line 10 is an endless conveying line, and the ingredient conveying line 10 is connect...
Embodiment 2
[0049] Such as Figure 5 As shown, the difference between the batching system for knitting production provided in this embodiment and the first embodiment is that the batching conveying line 10 used in this embodiment is not a circular conveying line, but includes first sub-conveyors arranged in a straight line. Line 11 and the second sub-conveying line 12, the first sub-conveying line 11 and the second sub-conveying line 12 are arranged side by side, and between the feed end of the first sub-conveying line 11 and the discharge end of the second sub-conveying line 12 And the discharge end of the first sub-conveyor line 11 and the feed end of the second sub-conveyor line 12 are respectively connected to each other by jacking and turning machines 13, that is, there are two jacking and turning machines 13, and each jacking and turning machine 13 Communicatively connected with the control module 90 respectively, and one of the jacking steering gears 13 is also connected with the f...
PUM
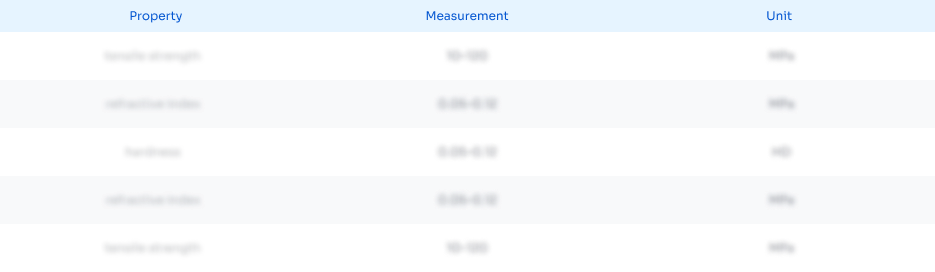
Abstract
Description
Claims
Application Information

- Generate Ideas
- Intellectual Property
- Life Sciences
- Materials
- Tech Scout
- Unparalleled Data Quality
- Higher Quality Content
- 60% Fewer Hallucinations
Browse by: Latest US Patents, China's latest patents, Technical Efficacy Thesaurus, Application Domain, Technology Topic, Popular Technical Reports.
© 2025 PatSnap. All rights reserved.Legal|Privacy policy|Modern Slavery Act Transparency Statement|Sitemap|About US| Contact US: help@patsnap.com