Air bearing
An air bearing and shaft technology, applied in the field of bearings, can solve the problems of rotor speed drop, rotor and bearing collision, danger, etc., and achieve the effect of maintaining stability, reducing flow and power consumption
- Summary
- Abstract
- Description
- Claims
- Application Information
AI Technical Summary
Problems solved by technology
Method used
Image
Examples
Embodiment Construction
[0050] In order to better understand the technical solutions of the present invention, the present invention will be further described below in conjunction with specific embodiments and accompanying drawings.
[0051] The present invention provides a side-by-side air bearing with an orifice, such as figure 1 As shown, it is an embodiment of an orifice setting, which includes a cylindrical body 11, and a plurality of concentric ring-shaped damping seats 12 are integrally formed on the periphery of one end of the body 11, and dampers 14 are installed radially on the damping seats 12. The seat 12 is radially provided with a mounting groove matching the damper 14 , and the damper seat 12 is provided with a throttle hole 13 passing through the body 11 in the radial direction. The part of the main body 11 with the damping seat 12 and the orifice 13 is the static pressure part of the air bearing, and the part of the main body 11 without the damping seat 12 and the orifice 13 is the d...
PUM
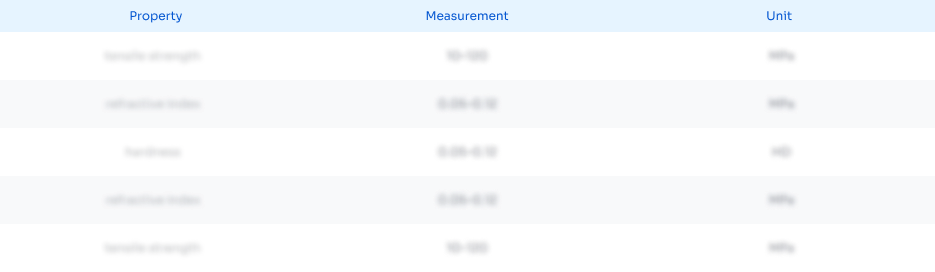
Abstract
Description
Claims
Application Information

- R&D
- Intellectual Property
- Life Sciences
- Materials
- Tech Scout
- Unparalleled Data Quality
- Higher Quality Content
- 60% Fewer Hallucinations
Browse by: Latest US Patents, China's latest patents, Technical Efficacy Thesaurus, Application Domain, Technology Topic, Popular Technical Reports.
© 2025 PatSnap. All rights reserved.Legal|Privacy policy|Modern Slavery Act Transparency Statement|Sitemap|About US| Contact US: help@patsnap.com