Roller kiln and smoke exhaust method of roller kiln based on furnace pressure control
A roller kiln and furnace pressure technology, applied in the direction of furnaces, furnace types, furnace components, etc., can solve problems such as lack of good measures, and achieve the goals of improving flue gas emission efficiency, reducing emission, and high flue gas emission efficiency Effect
- Summary
- Abstract
- Description
- Claims
- Application Information
AI Technical Summary
Problems solved by technology
Method used
Image
Examples
Embodiment Construction
[0026] The present invention will be described in further detail below in conjunction with the accompanying drawings and specific embodiments.
[0027] Such as figure 1 with figure 2 As shown, the roller kiln of this embodiment includes a furnace body 1 with a furnace 11 and a conveying device 2 installed in the furnace 11. The furnace 11 is provided with more than one smoke exhaust section 111, and the smoke exhaust section 111 is divided into two sections along the conveying device. 2 A plurality of sub-sections 100 connected in sequence in the conveying direction, and each sub-section 100 is provided with a smoke exhaust device 3 with adjustable exhaust speed. The furnace 11 of the roller kiln is provided with a smoke exhaust section 111, and the smoke exhaust section 111 is divided into a plurality of sub-sections 100, and each sub-section 100 is provided with a smoke exhaust device 3 with an adjustable exhaust speed, which can be adjusted according to the smoke exhaust....
PUM
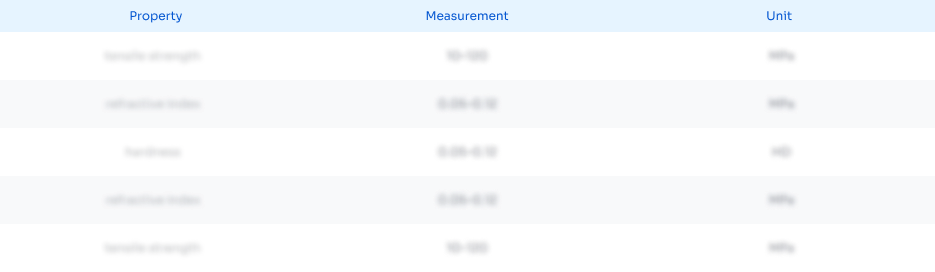
Abstract
Description
Claims
Application Information

- R&D Engineer
- R&D Manager
- IP Professional
- Industry Leading Data Capabilities
- Powerful AI technology
- Patent DNA Extraction
Browse by: Latest US Patents, China's latest patents, Technical Efficacy Thesaurus, Application Domain, Technology Topic, Popular Technical Reports.
© 2024 PatSnap. All rights reserved.Legal|Privacy policy|Modern Slavery Act Transparency Statement|Sitemap|About US| Contact US: help@patsnap.com