Continuous free bending precise forming method
A bending and precise technology, applied in the field of continuous free bending precision forming, can solve the problems of difficulty in guaranteeing the precision of bending forming and increasing difficulty of precise forming control, and achieve the effect of simple and feasible method, high production efficiency and reduced production cost
- Summary
- Abstract
- Description
- Claims
- Application Information
AI Technical Summary
Problems solved by technology
Method used
Image
Examples
Embodiment 1
[0024] Such as Figure 1-4 As shown, this embodiment takes the parabolic axis f(x) 1 =x 2 (-3≤x≤3) complex components as an example. Firstly, the bending axis is extracted on the complex bending member, there are n points on the axis, and each point corresponds to a bending radius R n , in the process of free bending, corresponding to an eccentricity U n and time t n , that is, at each time there is a corresponding eccentricity to control the free bending of the parabolic member. In this embodiment, 6 control points are selected on the parabolic axis, and the function relationship f(x) 1 =x 2 To determine the coordinates of the six control points P1 (-3, 9), P2 (-2, 4), P3 (-1, 1), P4 (1, 1), P5 (2, 4), P6 (3 , 9), and calculate the bending radius R n , the eccentricity and movement speed of the bending die are determined through the calculation of each analytical formula of the free bending forming process, so as to determine the motion trajectory, and the free bendin...
Embodiment 2
[0030] The present invention uses a self-defined continuous curve f(x) 2 as an example. Firstly, the bending axis is extracted from the complex curved member, and the bending radius changes with the increase of the arc length, and the bending radius will increase or decrease by 20mm for every 50mm increase in the arc length. The bending radius of the initial point of the curve segment is 260mm, there are n points on the axis, and each point corresponds to a bending radius R n , in the process of free bending, corresponding to an eccentricity U n and time t n , that is, there is a corresponding eccentricity at each time to control the free bending forming of complex components. For example, select 6 control points on the custom complex axis, and use the function relationship f(x) 2 The law to determine the bending radius R of the six control points n , respectively for R 1 =260mm, R 2 =240mm, R 3 =220mm, R 4 = 200mm, R 5 =180mm, R 6 =160mm, the eccentricity and movem...
PUM
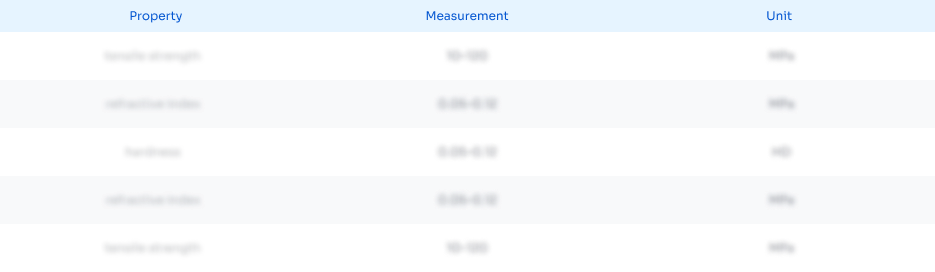
Abstract
Description
Claims
Application Information

- Generate Ideas
- Intellectual Property
- Life Sciences
- Materials
- Tech Scout
- Unparalleled Data Quality
- Higher Quality Content
- 60% Fewer Hallucinations
Browse by: Latest US Patents, China's latest patents, Technical Efficacy Thesaurus, Application Domain, Technology Topic, Popular Technical Reports.
© 2025 PatSnap. All rights reserved.Legal|Privacy policy|Modern Slavery Act Transparency Statement|Sitemap|About US| Contact US: help@patsnap.com