Short-base sensor for ship structure stress monitoring and using method thereof
A technology of structural stress and sensor, applied in the field of disaster prevention and monitoring of marine ships and stress sensor, can solve the problems of damage and destruction of hull structure, and achieve the effect of good specification, small structure, flexible debugging and maintenance
- Summary
- Abstract
- Description
- Claims
- Application Information
AI Technical Summary
Problems solved by technology
Method used
Image
Examples
Embodiment 1
[0041] A short-base sensor used for stress monitoring of ship structures comprises: a connecting device, a fixing device, a sealing device and a stress-sensitive element.
[0042] The connecting device is composed of a connecting pipe 3 , an upper protective pipe 5 , a lower protective pipe 6 , and an optical fiber sticking bearing block 7 . There is a connecting tube 3 at both ends, and an optical fiber sticking bearing block 7 is placed in it. The two connecting tubes 3 are connected by a protective tube, and the protective tube is fixedly connected by the upper protective tube 5 and the lower protective tube 6 through screw holes. The connecting parts of the pipes are all sealed with watertight grooves, and rubber sealing rings are inserted into the watertight grooves to ensure the watertightness of the connections.
[0043] The fixing device includes: a sensor fixing block 2 and a fixing screw hole 8 of the pasting block. Wherein the fixing screw holes 8 of the sticking b...
Embodiment 2
[0047] The short-base sensor for ship structure stress monitoring is characterized in that the sensor system includes: a connecting device, a fixing device, a sealing device and a stress sensitive element. The connection device consists of a connecting tube 3, an upper protection tube 5, a lower protection tube 6, and an optical fiber adhesive bearing block 7; the fixing device includes a sensor fixing block 2 and an adhesive block fixing screw hole 8; the sealing device includes an optical fiber waterproof aviation plug connection plate 1, The sealing plate 4, the optical fiber waterproof aviation socket 11 and the aviation insertion fixing hole 12, the connecting part is provided with a sealing port, and a multi-layer sealing ring is provided inside to play a watertight role and prevent the sensor from monitoring the stress due to water ingress.
[0048] Wherein the stress sensitive element is composed of a single fiber grating and a temperature compensation grating. The def...
Embodiment 3
[0050] Methods of use include:
[0051] (1) After the sensor is installed and the top wire of the fiber grating is connected to the demodulator through a waterproof aviation plug, if the hull part of the installation position is subjected to external force, the sensor will also be deformed accordingly, and it will be pasted on the bearing blocks at both ends The fiber between 8 will also be deformed, which will cause the wavelength of the fiber grating to change.
[0052] (2) The stress change of the ship hull is reflected on the demodulator through the change of the fiber grating wavelength, because the deformation of the fiber grating is basically in a linear relationship with the deformation of the fiber grating, so through the compensation algorithm of the demodulator, the stress change of the hull structure and The wavelength change of the fiber grating is also basically linearly proportional.
PUM
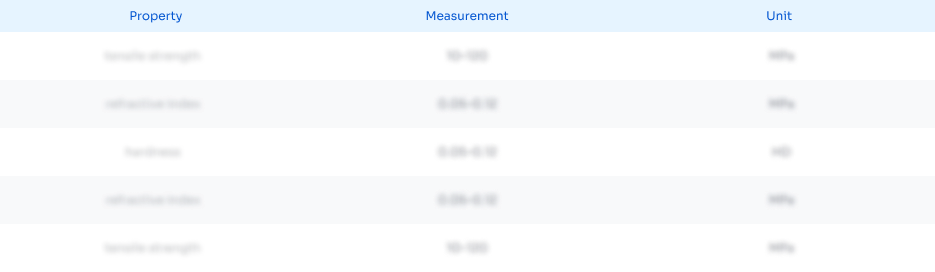
Abstract
Description
Claims
Application Information

- R&D Engineer
- R&D Manager
- IP Professional
- Industry Leading Data Capabilities
- Powerful AI technology
- Patent DNA Extraction
Browse by: Latest US Patents, China's latest patents, Technical Efficacy Thesaurus, Application Domain, Technology Topic, Popular Technical Reports.
© 2024 PatSnap. All rights reserved.Legal|Privacy policy|Modern Slavery Act Transparency Statement|Sitemap|About US| Contact US: help@patsnap.com