Preparation method of water-based superfine fiber synthetic leather
A technology of superfine fiber and synthetic leather, which is applied in fiber processing, textiles and papermaking, etc. It can solve the problems of poor leather feel, tight and inflexible surface of synthetic leather, etc., and achieve the effect of strong leather feeling and full hand feeling
- Summary
- Abstract
- Description
- Claims
- Application Information
AI Technical Summary
Problems solved by technology
Method used
Examples
Embodiment 1
[0023] (1) Coat the surface of the water-soluble polyester / polyamide sea-island fiber nonwoven with a water-based hydrophobic additive, and then dry it at 100°C. The hydrophobic additive after drying and curing accounts for 2%, thereby making the base cloth A of surface hydrophobic pretreatment;
[0024] Wherein, the water-based hydrophobic additive is the water-based hydrophobic agent DC-51 of American Dow Corning.
[0025] (2) Evenly immerse the base fabric A prepared in step (1) into the water-based polyurethane impregnated resin for 5 minutes, and then pass it through the rollers to control the impregnation amount of the polyurethane impregnated resin to 60% of the weight of the nonwoven fabric, and then heat it at 100°C Drying treatment is carried out under certain conditions to solidify the polyurethane impregnated resin, so as to obtain the composite base cloth B;
[0026] Among them, the waterborne polyurethane impregnation resin is Covestro's waterborne polyurethane ...
Embodiment 2
[0030] (1) Coat the surface of the water-soluble polyester / polyamide sea-island fiber nonwoven with a water-based hydrophobic additive, and then dry it at 110°C. The hydrophobic additive after drying and curing accounts for 3%, thereby making the base cloth A of surface hydrophobic pretreatment;
[0031] Wherein, the water-based hydrophobic additive is the water-based hydrophobic agent IE-6683 of Dow Corning in the United States.
[0032] (2) Evenly immerse the base fabric A prepared in step (1) into the water-based polyurethane impregnated resin for 5 minutes, and then pass through the rollers to control the impregnation amount of the polyurethane impregnated resin to 50% of the weight of the nonwoven fabric, and then heat it at 110°C Drying treatment is carried out under certain conditions to solidify the polyurethane impregnated resin, so as to obtain the composite base cloth B;
[0033] Among them, the waterborne polyurethane impregnation resin is Covestro's waterborne po...
Embodiment 3
[0037](1) Coat the surface of the water-soluble polyester / polyester island-in-the-sea fiber nonwoven fabric with a water-based hydrophobic additive, and then dry it at 90°C. The hydrophobic additive after drying and curing accounts for 3%, thereby making the base cloth A of surface hydrophobic pretreatment;
[0038] Among them, the water-based hydrophobic additive is Chengdu Zhaojiang Technology's water-based hydrophobic agent HY-4100.
[0039] (2) Evenly immerse the base fabric A prepared in step (1) into the water-based polyurethane impregnated resin for 6 minutes, and then pass through the rollers to control the impregnation amount of the polyurethane impregnated resin to 60% of the weight of the nonwoven fabric, and then heat it at 120°C Drying treatment is carried out under certain conditions to solidify the polyurethane impregnated resin, so as to obtain the composite base cloth B;
[0040] Among them, the waterborne polyurethane impregnation resin is Covestro's waterbo...
PUM
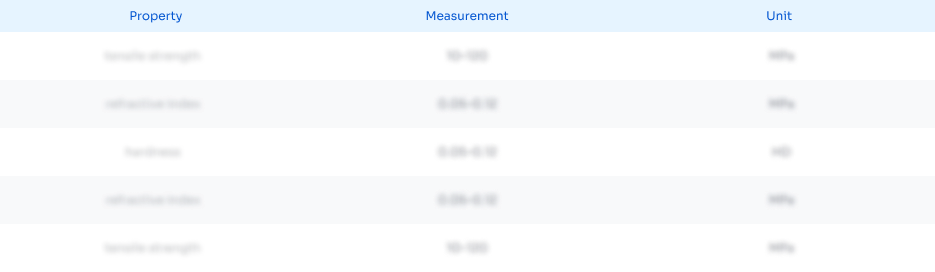
Abstract
Description
Claims
Application Information

- R&D Engineer
- R&D Manager
- IP Professional
- Industry Leading Data Capabilities
- Powerful AI technology
- Patent DNA Extraction
Browse by: Latest US Patents, China's latest patents, Technical Efficacy Thesaurus, Application Domain, Technology Topic, Popular Technical Reports.
© 2024 PatSnap. All rights reserved.Legal|Privacy policy|Modern Slavery Act Transparency Statement|Sitemap|About US| Contact US: help@patsnap.com