Torque control method and system for electric power-assisted transport vehicle
A technology of torque control and electric power assist, which is applied in the field of torque control methods and systems for electric power-assisted transport vehicles, can solve problems such as complex calculation of torque control methods, achieve good steering control road feeling, and solve the effects of complex calculations
- Summary
- Abstract
- Description
- Claims
- Application Information
AI Technical Summary
Problems solved by technology
Method used
Image
Examples
Embodiment 1
[0030] 1) When turning, detect the torque of the steering wheel; the torque sensor 2 detects the torque of the steering wheel in real time, and the control unit receives the torque sensor of the steering wheel;
[0031] 2) Judgment: If the current torque is less than the first set torque value, the power assist characteristic of the power assist motor is zero; if the current torque is greater than the first set torque value and less than the second set torque value, the power assist motor The boost characteristic of the motor increases with the increase of the current torque. If the current torque is greater than the second set torque value, the boost characteristic of the boost motor is a constant value; combined with the judgment of the boost characteristic curve, the current boost current I , the power assist characteristic curve function is:
[0032]
[0033] Among them, T d0 is the first set torque value, and the first set torque value represents the corresponding ste...
Embodiment 2
[0038] 1) When turning, detect the torque of the steering wheel; the torque sensor 2 detects the torque of the steering wheel in real time, the vehicle speed sensor Va detects the current vehicle speed, and the control unit receives the signals detected by the steering wheel torque sensor and the speed sensor;
[0039] 2) Judgment: If the current torque is less than the first set torque value, the power assist characteristic of the power assist motor is zero; if the current torque is greater than the first set torque value and less than the second set torque value, the power assist motor The boost characteristic of the motor increases with the increase of the current torque. If the current torque is greater than the second set torque value, the boost characteristic of the boost motor is a constant value; combined with the judgment of the boost characteristic curve, the current boost current I ,Such as figure 2 As shown, the assist characteristic curve function is:
[0040] ...
PUM
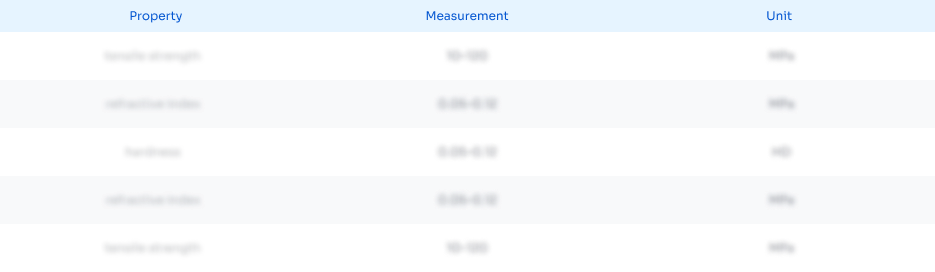
Abstract
Description
Claims
Application Information

- Generate Ideas
- Intellectual Property
- Life Sciences
- Materials
- Tech Scout
- Unparalleled Data Quality
- Higher Quality Content
- 60% Fewer Hallucinations
Browse by: Latest US Patents, China's latest patents, Technical Efficacy Thesaurus, Application Domain, Technology Topic, Popular Technical Reports.
© 2025 PatSnap. All rights reserved.Legal|Privacy policy|Modern Slavery Act Transparency Statement|Sitemap|About US| Contact US: help@patsnap.com