Magnetic shoe sintering electric kiln rotary line extension device and implementation method thereof
A magnetic tile sintering and extension device technology, applied in the direction of conveyor control devices, transportation and packaging, conveyor objects, etc., can solve problems such as difficulty in recruiting employees, achieve the effects of reducing labor intensity, low equipment cost, and reducing usage
- Summary
- Abstract
- Description
- Claims
- Application Information
AI Technical Summary
Problems solved by technology
Method used
Image
Examples
Embodiment
[0029] see Figure 1-4 , the present invention provides the following technical solutions: a magnetic tile sintering electric kiln rotating line extension device, including an electric kiln 1, the feeding end of the electric kiln 1 is provided with a feeding rotating line 12, and the feeding end of the electric kiln 1 is provided with a lower The feeding rotary line 2, the unloading rotary line 2 and the loading rotary line 12 are connected through the storage conveyor line 8, and the end of the blanking rotary line 2 close to the storage conveyor line 8 is provided with the first unloading station 3, and the feeding rotary The end of the line 12 close to the storage conveying line 8 is provided with a second loading station 9, and the side of the storage conveying line 8 far away from the electric kiln 1 is respectively provided with a second unloading station 5 and a first feeding station 6. A first robot 4 and a second robot 7 are respectively provided on the side of the co...
Embodiment 2
[0045] The difference between this embodiment and Embodiment 1 lies in: specifically, one more station is added to one side of the second unloading station 5 and the first loading station 6 respectively.
[0046] By adopting the above technical scheme, two workers are used to unload the magnetic tiles, and two workers are used to load the magnetic tiles, thereby reducing the labor intensity of the workers.
[0047] To sum up, the present invention can extend the rotary line by setting the storage conveying line, and carry out loading and unloading by robots, so as to realize the elimination of the workers who load the blanks of the late shift magnetic tiles and the unloaders who burn the finished magnetic tiles; The temperature of the working environment of the kiln is high. When the workers are working, the refrigeration facilities such as air conditioners and fans on the posts need to work. The workers in the present invention only need to work for eight hours, and the refrig...
PUM
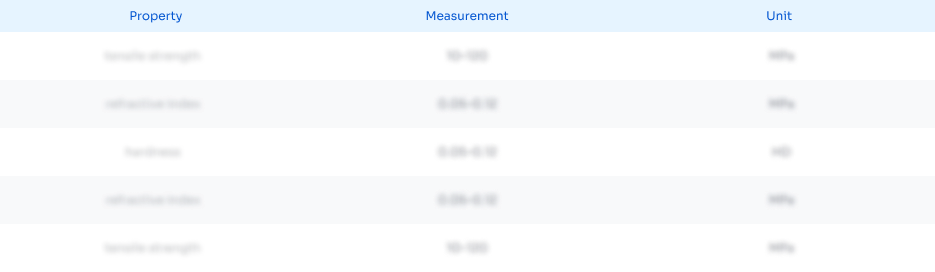
Abstract
Description
Claims
Application Information

- R&D Engineer
- R&D Manager
- IP Professional
- Industry Leading Data Capabilities
- Powerful AI technology
- Patent DNA Extraction
Browse by: Latest US Patents, China's latest patents, Technical Efficacy Thesaurus, Application Domain, Technology Topic, Popular Technical Reports.
© 2024 PatSnap. All rights reserved.Legal|Privacy policy|Modern Slavery Act Transparency Statement|Sitemap|About US| Contact US: help@patsnap.com