Combined core-pulling mechanism and injection mold
A core-pulling mechanism and fixed template technology, applied in the field of molds, can solve problems such as complex core-pulling process, low product molding quality, and complex structure
- Summary
- Abstract
- Description
- Claims
- Application Information
AI Technical Summary
Problems solved by technology
Method used
Image
Examples
no. 1 example
[0029] Please refer to figure 1 , figure 2 , image 3 and Figure 4 , the embodiment of the present invention provides a combined core-pulling mechanism 100 for core-pulling molding of products. It can complete core-pulling actions in two different directions at the same time, simplify the core-pulling structure, reduce occupied space, reduce mold manufacturing costs, and make the core-pulling process stable and reliable, ensuring product molding quality. In this embodiment, the combined core-pulling mechanism 100 is used for core-pulling a product containing buckles and ribs at the same time, wherein the core-pulling direction of the buckle and the core-pulling direction of the ribs are perpendicular to each other, and the combined core-pulling mechanism 100 can Core-pulling molding is performed in both directions at the same time.
[0030] The combined core pulling mechanism 100 includes a fixed template 110, a movable template 120, a shovel base 130, an inclined guide ...
no. 2 example
[0046] Please refer to Figure 10 , the present invention provides an injection mold 10 for producing plastic products. The injection mold 10 includes a combined core pulling mechanism 100 , a fixed mold seat plate 400 and a movable mold seat plate 300 . Wherein, the basic structure, principle and technical effect of the combined core-pulling mechanism 100 are the same as those of the first embodiment. For a brief description, for parts not mentioned in this embodiment, reference may be made to the corresponding content in the first embodiment.
[0047] In this embodiment, the movable mold base plate 300 is connected to the movable platen 120, the fixed mold base plate 400 is connected to the fixed mold plate 110, and the movable mold base plate 300 and the fixed mold base plate 400 are relatively installed on two sides of the injection molding machine (not shown). On the side, the injection molding machine can drive the movable platen 120 close to or away from the fixed plat...
PUM
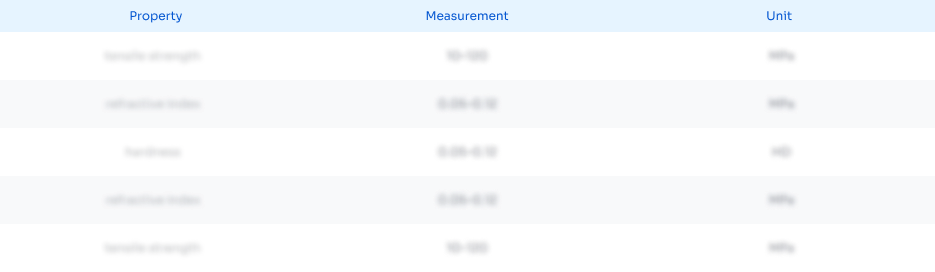
Abstract
Description
Claims
Application Information

- R&D Engineer
- R&D Manager
- IP Professional
- Industry Leading Data Capabilities
- Powerful AI technology
- Patent DNA Extraction
Browse by: Latest US Patents, China's latest patents, Technical Efficacy Thesaurus, Application Domain, Technology Topic, Popular Technical Reports.
© 2024 PatSnap. All rights reserved.Legal|Privacy policy|Modern Slavery Act Transparency Statement|Sitemap|About US| Contact US: help@patsnap.com