Distribution table for plastic trays
A technology of plastic trays and dividing tables, which is applied in the stacking of objects, destacking and packaging of objects, etc., can solve the problems such as the adsorption of trays together and the low efficiency of manual separation, and achieve the effect of improving efficiency.
- Summary
- Abstract
- Description
- Claims
- Application Information
AI Technical Summary
Problems solved by technology
Method used
Image
Examples
Embodiment 1
[0020] see Figure 1 to Figure 3 , the present embodiment provides a plastic tray splitting table, firstly, a splitting table body 1 is provided, a retrieving station and a sheeting station are arranged on it, and a plurality of plastic tray bodies 2 are stacked on the retrieving station , a splitting mechanism 3 is installed on the splitting station, and the splitting mechanism 3 includes a splitting plate 31 and a plurality of splitting suckers 32, and the splitting plate 31 is fixedly installed on the splitting station, and a plurality of splitting suckers 32 It is detachably mounted on the splitting plate 31, and the retrieving device 4 is erected on the splitting table body 1. The retrieving device 4 includes a translation mechanism 41 and a lifting mechanism 42, and the translation mechanism 41 includes a carriage 411 and a first driving part 412 The first driving part 412 drives the carriage 411 to slide between the reclaiming station and the splitting station, the lift...
Embodiment 2
[0026] see Figure 1 to Figure 3 , the figure shows a plastic tray sheeting table provided by Embodiment 2 of the present invention. On the basis of the above-mentioned embodiments, this embodiment further makes the following technical solutions as improvements: In Embodiment 1 On the basis, a sensor is added, and the sensor is installed on the main body of the sheeting table 1. When the plastic tray body is adsorbed on the sheeting mechanism 3, the sensor can identify and send the signal to the retrieving device 4, and the retrieving device 4 continues to transfer the sheeting mechanism 3 The plastic tray body on the top is absorbed and enters the next process.
[0027] The above-mentioned structure can fill in the defect that the plastic tray body on the splitting mechanism 3 cannot be automatically removed, thereby improving the degree of automation.
Embodiment 3
[0029] see Figure 1 to Figure 3, the figure shows a plastic tray sheeting table provided by the third embodiment of the present invention. This embodiment further makes the following technical solutions as improvements on the basis of the above-mentioned embodiments: In the first embodiment On the basis, an alarm is added, and the alarm is installed on the splitting mechanism 3. When the plastic tray body is adsorbed on the splitting mechanism 3, the alarm will send out an alarm to notify the staff to come and take off the plastic tray body on the splitting mechanism 3, thereby Guarantee the smooth operation of the machine.
PUM
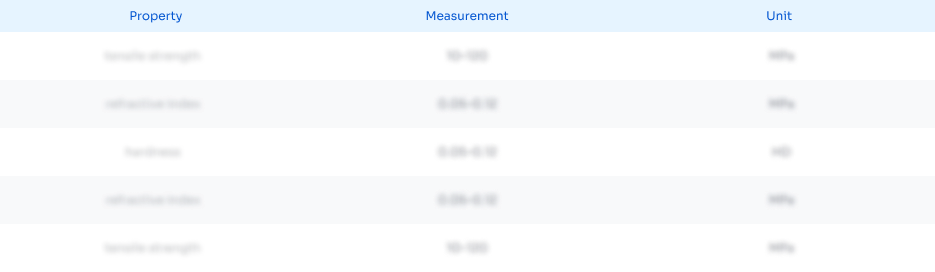
Abstract
Description
Claims
Application Information

- R&D Engineer
- R&D Manager
- IP Professional
- Industry Leading Data Capabilities
- Powerful AI technology
- Patent DNA Extraction
Browse by: Latest US Patents, China's latest patents, Technical Efficacy Thesaurus, Application Domain, Technology Topic, Popular Technical Reports.
© 2024 PatSnap. All rights reserved.Legal|Privacy policy|Modern Slavery Act Transparency Statement|Sitemap|About US| Contact US: help@patsnap.com