Polyhedral groove grease coating equipment
A technology of polyhedron and grease, which is applied to the device and coating of the surface coating liquid, can solve the problems of low work efficiency, narrow and deep polyhedral groove space, and narrow operating space, so as to achieve simple, compact and safe equipment structure Reliable semi-automatic, solve the effect of narrow operating space
- Summary
- Abstract
- Description
- Claims
- Application Information
AI Technical Summary
Problems solved by technology
Method used
Image
Examples
Embodiment Construction
[0033] The present invention will be further described below in conjunction with the accompanying drawings and embodiments.
[0034] Also refer to figure 1 , figure 2 , image 3 , Figure 4 , Figure 5 , Image 6 , Figure 7 , Figure 8 , Figure 9 , Figure 10 , Figure 11 , Figure 12 , Figure 13 , Figure 14 ,in, figure 1 It is a schematic diagram of the overall structure of the polyhedral groove coating grease equipment of the present invention; figure 2 for figure 1 A schematic diagram of the internal structure of the power trolley assembly 21 of the oiling mechanism assembly 2 of the polyhedral groove coating grease equipment shown; image 3 for figure 1 A schematic diagram of the internal structure of the single-axis transmission oiling assembly 22 of the oiling mechanism assembly 2 of the polyhedral groove coating grease equipment shown; Figure 4 for image 3 The axonometric schematic diagram of the greased slider 226 of the single shaft transmiss...
PUM
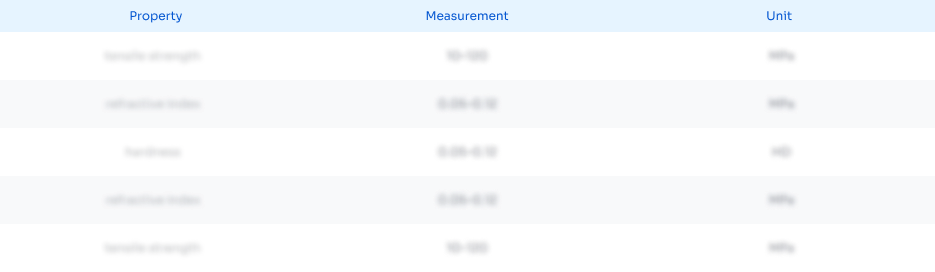
Abstract
Description
Claims
Application Information

- R&D
- Intellectual Property
- Life Sciences
- Materials
- Tech Scout
- Unparalleled Data Quality
- Higher Quality Content
- 60% Fewer Hallucinations
Browse by: Latest US Patents, China's latest patents, Technical Efficacy Thesaurus, Application Domain, Technology Topic, Popular Technical Reports.
© 2025 PatSnap. All rights reserved.Legal|Privacy policy|Modern Slavery Act Transparency Statement|Sitemap|About US| Contact US: help@patsnap.com