Cutter shaft optimization method for curved surface numerical control machining ball-end milling cutter abrasion control
An optimization method and technology of ball end milling cutter, applied in the field of CAD/CAM, can solve problems such as tool failure too fast
- Summary
- Abstract
- Description
- Claims
- Application Information
AI Technical Summary
Problems solved by technology
Method used
Image
Examples
Embodiment Construction
[0047] The effectiveness of the tool axis optimization method of the proposed curved surface CNC machining ball nose cutter wear control is verified below for the present invention in conjunction with the accompanying drawings, and relevant examples have been designed for verification. The constructed curved surface is as follows figure 1 shown. The material used for the workpiece is a nickel-based superalloy. Other parameters in the experiment are as follows:
[0048] Tool: Ball-end knife, radius R12mm, 4 blades
[0049] depth of cut d c : 0.3mrn
[0050] Spindle speed N: 700rpm
[0051] Feed per tooth F z : 0.3mrn
[0052] Processing method: down milling
[0053] Tool wear threshold: 0.2mrn
[0054] A tool axis optimization method for wear control of ball end milling cutters in NC machining of curved surfaces, such as figure 2 shown, including the following steps:
[0055] 1) Calculate the tool-workpiece engagement area at all tool positions. Extract the generate...
PUM
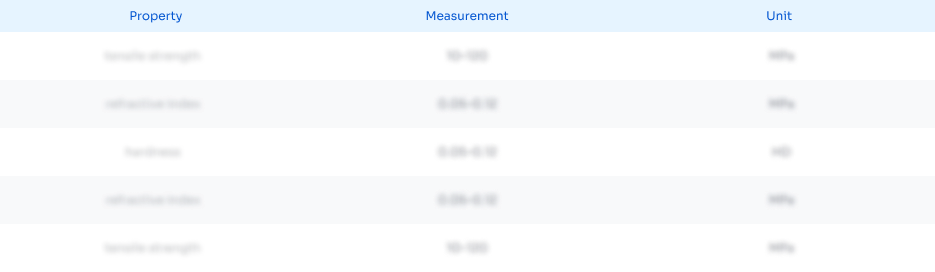
Abstract
Description
Claims
Application Information

- R&D
- Intellectual Property
- Life Sciences
- Materials
- Tech Scout
- Unparalleled Data Quality
- Higher Quality Content
- 60% Fewer Hallucinations
Browse by: Latest US Patents, China's latest patents, Technical Efficacy Thesaurus, Application Domain, Technology Topic, Popular Technical Reports.
© 2025 PatSnap. All rights reserved.Legal|Privacy policy|Modern Slavery Act Transparency Statement|Sitemap|About US| Contact US: help@patsnap.com