Rotary type magnetorheological damper capable of outputting asymmetric damping
A magnetorheological damper, rotary technology, applied in the field of mechanical vibration reduction, can solve problems such as increasing the dependence of complex sensing systems and control systems
- Summary
- Abstract
- Description
- Claims
- Application Information
AI Technical Summary
Problems solved by technology
Method used
Image
Examples
Embodiment Construction
[0016] figure 1 It is a structural schematic diagram of the present invention; as shown in the figure, a rotary magneto-rheological damper capable of outputting asymmetrical damping includes an outer cylinder 2, a left end cover 1 fixedly connected to the left end of the outer cylinder 2, and an outer The right end of the cylinder 2 is fixedly connected to the right end cover 3; the inside of the outer cylinder 2 is arranged in sequence from outside to inside (from outside to inside, that is, from the inner wall of the outer cylinder to the axis of the outer cylinder as shown in the figure). Core 5, iron core magnetic isolation cylinder 7, inner iron core 8, inner cylinder 21 and magnetorheological fluid push rod 10 (outer iron core 5, iron core magnetic isolation cylinder 7 and inner iron core 8 are fixedly connected way, and there is no gap between the three); the outer iron core 5 and the outer cylinder 2 form a first annular channel 19 for the circulation of magnetorheolog...
PUM
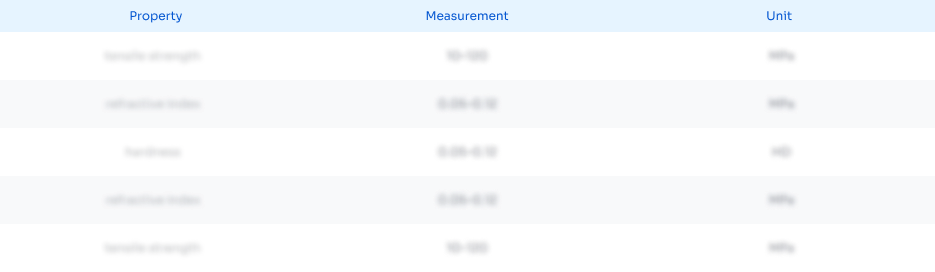
Abstract
Description
Claims
Application Information

- R&D Engineer
- R&D Manager
- IP Professional
- Industry Leading Data Capabilities
- Powerful AI technology
- Patent DNA Extraction
Browse by: Latest US Patents, China's latest patents, Technical Efficacy Thesaurus, Application Domain, Technology Topic, Popular Technical Reports.
© 2024 PatSnap. All rights reserved.Legal|Privacy policy|Modern Slavery Act Transparency Statement|Sitemap|About US| Contact US: help@patsnap.com