Omni-directional movable platform for automatic transportation and application thereof
An omnidirectional mobile and automatic transportation technology, applied in transportation and packaging, motor vehicles, electric steering mechanisms, etc., can solve the problems of large vibration of the mobile platform, difficulty in ensuring accuracy, and obstacle-crossing ability limitations, and achieve high-speed and high-precision movement. Control and eliminate the effect of large number and strong load capacity
- Summary
- Abstract
- Description
- Claims
- Application Information
AI Technical Summary
Problems solved by technology
Method used
Image
Examples
Embodiment 1
[0033] like Figure 1-5 As shown, the present embodiment provides an omnidirectional mobile platform for automatic transportation, including a mobile platform frame, a drive mechanism, a steering mechanism, a steering drive mechanism and wheels;
[0034] There are four wheels arranged under the frame of the mobile platform, two of which are connected through half shafts, couplings, and front wheel shafts, and the other two wheels are connected through half shafts, couplings, and rear wheel shafts. There is a front spur gear, and a rear spur gear is arranged on the rear axle, and the front spur gear and the rear spur gear are connected through a third synchronous belt;
[0035] The driving mechanism is installed on the frame of the mobile platform, and is connected to the small bevel gear set on the front wheel shaft through gear transmission;
[0036] The steering mechanism includes four steering gears, the steering power gear, and the steering power pinion; the steering driv...
Embodiment 2
[0042]A kind of working method of omnidirectional mobile platform for automatic transportation as described in embodiment 1, comprises the following steps:
[0043] The driving mechanism is started, and the front wheel shaft 5 is driven to rotate through the gear transmission, thereby driving the rear wheel shaft 6 to rotate synchronously, driving the wheels to move forward;
[0044] When turning is needed, the steering drive mechanism starts, and the four wheels are synchronously driven by the steering power gear 11, the steering power pinion 12, the steering gear 20, and the support shaft 13 to rotate at an angle to realize steering.
[0045] The angular rotation designed in the present invention realizes zero-radius (no offset) rotation, in-situ rotation, and rotation around its own rotation center (geometric center), which has a certain rotation radius compared with ordinary vehicle rotation. This saves space and, in a warehouse environment, has certain advantages.
[004...
PUM
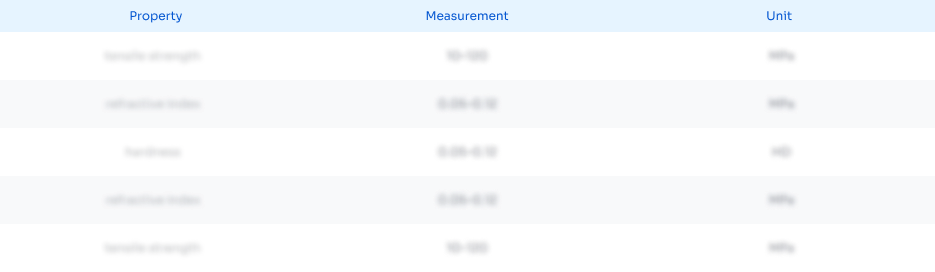
Abstract
Description
Claims
Application Information

- Generate Ideas
- Intellectual Property
- Life Sciences
- Materials
- Tech Scout
- Unparalleled Data Quality
- Higher Quality Content
- 60% Fewer Hallucinations
Browse by: Latest US Patents, China's latest patents, Technical Efficacy Thesaurus, Application Domain, Technology Topic, Popular Technical Reports.
© 2025 PatSnap. All rights reserved.Legal|Privacy policy|Modern Slavery Act Transparency Statement|Sitemap|About US| Contact US: help@patsnap.com