A Climbing Robot for Pipeline Inspection
A pipeline detection and robot technology, applied in the field of climbing robots, can solve the problems of collision between camera equipment and devices, inability to immediately stop and lock the climbing feet, detection errors, etc., and achieve the effect of not easy to lubricate impurities
- Summary
- Abstract
- Description
- Claims
- Application Information
AI Technical Summary
Problems solved by technology
Method used
Image
Examples
Embodiment
[0024] see Figure 1-Figure 5 , the present invention provides a climbing robot for pipeline detection, the structure of which includes a mounting bracket 1, a brake mechanism 2, a camera 3, a driving box 4, and walking wheels 5, and four walking wheels are installed on both sides of the driving box 4. Wheel 5, the top surface of the driving box 4 is provided with a mounting bracket 1, the mounting bracket 1 and the driving box 4 are locked by screws, the camera 3 is installed on the mounting bracket 1, and the walking wheel 5 and the driving box 4 A camera 3 is mounted on the driving spindle 10 between them.
[0025] The brake mechanism 2 is provided with a mounting plate 6, a static friction plate 7, a mounting hole 8, and a dynamic friction plate 9. The two ends of one side of the mounting plate 6 are provided with mounting holes 8, and the mounting plate 6 is provided with a static friction plate 7. , the static friction plate 7 is fixedly connected to the mounting plate ...
PUM
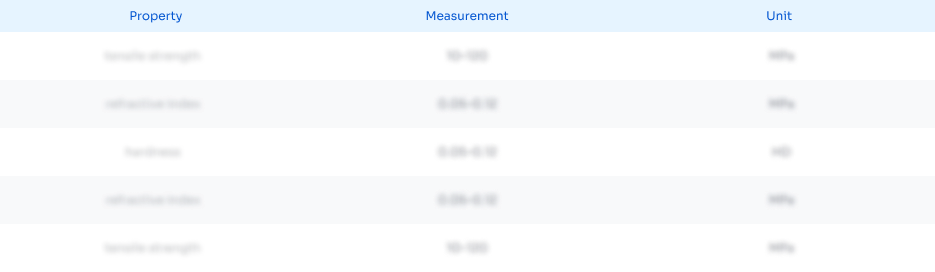
Abstract
Description
Claims
Application Information

- R&D Engineer
- R&D Manager
- IP Professional
- Industry Leading Data Capabilities
- Powerful AI technology
- Patent DNA Extraction
Browse by: Latest US Patents, China's latest patents, Technical Efficacy Thesaurus, Application Domain, Technology Topic, Popular Technical Reports.
© 2024 PatSnap. All rights reserved.Legal|Privacy policy|Modern Slavery Act Transparency Statement|Sitemap|About US| Contact US: help@patsnap.com