Composite material plate pre-compression clamping method
A composite material board and composite material technology, applied in the field of composite material board testing, can solve the problems of cumbersome assembly, difficult operation, large size, etc., and achieve the effect of compact and compact overall structure, simplified device structure, and promotion of influence rules
- Summary
- Abstract
- Description
- Claims
- Application Information
AI Technical Summary
Problems solved by technology
Method used
Image
Examples
Embodiment Construction
[0036] Please refer to the attached figure 1 to attach Figure 4 As shown, the present invention is a composite material plate pre-compression clamping device for compressing and clamping a composite material plate 10, which consists of a load plate 1, a horizontal clamp group 2, a compression block I3, a compression block II4, and a tension sensor 5 And several parts such as ejection bolt 6 are formed.
[0037] Wherein, four through holes 11 are provided at the corners of the four directions of the carrying board 1 , and the distances from the crossing lines of the edges are the same. Fixing bolts (not shown) are pierced through the through holes 11 to position the bearing plate 1 . A plate groove 12 is arranged on the carrying plate 1 ; a preload groove 13 is arranged on one side of the plate groove 12 . The preload groove 13 is located in the longitudinal direction of the composite material plate 10 and communicates with the plate groove 12 .
[0038] Further, the depth...
PUM
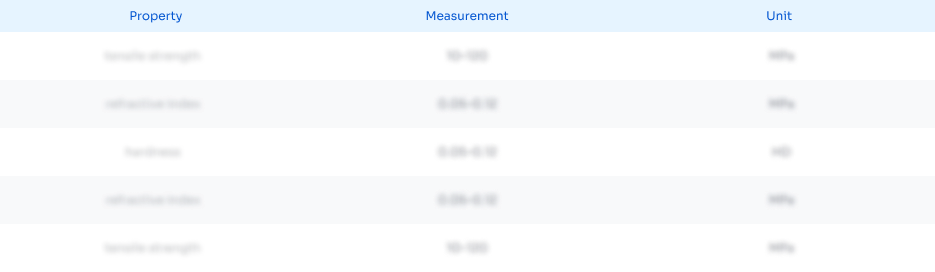
Abstract
Description
Claims
Application Information

- R&D Engineer
- R&D Manager
- IP Professional
- Industry Leading Data Capabilities
- Powerful AI technology
- Patent DNA Extraction
Browse by: Latest US Patents, China's latest patents, Technical Efficacy Thesaurus, Application Domain, Technology Topic, Popular Technical Reports.
© 2024 PatSnap. All rights reserved.Legal|Privacy policy|Modern Slavery Act Transparency Statement|Sitemap|About US| Contact US: help@patsnap.com