Self-film-cutting type aluminum profile double-side-face synchronous film pasting machine
An aluminum profile and film laminating machine technology, which is applied in the direction of winding strips, packaging, thin material processing, etc., can solve the problems of low lamination fastness, low lamination efficiency, insufficient contact, etc., to reduce lamination stations, improve The effect of film sticking efficiency and cost reduction
- Summary
- Abstract
- Description
- Claims
- Application Information
AI Technical Summary
Problems solved by technology
Method used
Image
Examples
Embodiment 1
[0057] Such as Figure 1-3 As shown, this embodiment discloses a self-cutting film-type aluminum profile double-sided synchronous film laminating machine, including a frame 1, a pair of limit rollers 2, a guide roller 3, a roll film roller 41, a contact roller 51, a transmission mechanism 52, a cutting Knife 53, guide film roller 54, pressure film roller 61, telescoping rod 62, clamping mechanism 63, elastic device. The limit pair of rollers 2 is located at the front end of the frame 1, and is used to limit the position of the aluminum profile 9 input to the film laminating machine. The guide rollers 3 are rotatably connected with the frame 1, and several guide rollers 3 are distributed from the front end of the frame 1 to the rear end of the frame 1 at intervals. In this embodiment, one or several guide rollers 3 at the front are used as driving rollers, driven by a motor to rotate, and other guide rollers 3 are used as driven rollers. Certainly, the present invention is no...
Embodiment 2
[0072] Such as Image 6 As shown, the difference between this embodiment and the above-mentioned embodiment is that an installation groove 12 is provided on the top of the front end of the frame 1, the bottom of the guide film roller 54 is fixed on the installation groove 12, and the cutting knife mounting part 523 is connected with the installation groove 12. They are rotatably connected by the first connecting shaft. Both ends of the transmission member 522 are respectively hinged to the bottom of the cutting knife mounting part 523 and the bottom of the contact roller mounting part 521 .
[0073] When actually carrying out the side film sticking, since the distance between the bottom of the film and the top surface of the frame 1 is small, in order to ensure that the transmission mechanism 52 has enough installation space and the needs of low-level installation, the present invention places the top of the front end of the frame 1 The installation groove 12 is opened, and t...
Embodiment 3
[0075] Such as Figure 10 , 11 As shown, the difference between the present embodiment and the above-mentioned embodiments is that: a first guide groove 13 is provided on the top of the front end of the frame 1, and the guiding direction of the first guide groove 13 is perpendicular to the direction in which the aluminum profile 9 is conveyed. The bottom of the contact roller mounting part 521 is slidingly matched with the first guide groove 13 . The inner bottom of the mounting groove 12 defines a second guiding groove 121 , and the guiding direction of the second guiding groove 121 is consistent with the guiding direction of the first guiding groove 13 . A sliding block 122 is slidably fitted on the second guide groove 121 , the bottom of the film guiding roller 54 is fixed on the sliding block 122 , and the cutting knife mounting part 523 is rotationally connected with the sliding block 122 through a first connecting shaft.
[0076] Since the contact roller 51 of the pres...
PUM
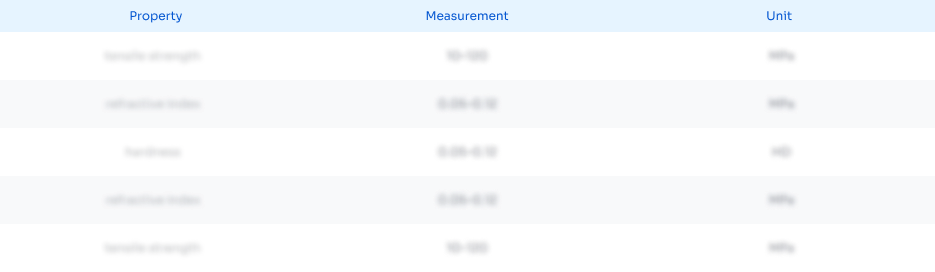
Abstract
Description
Claims
Application Information

- Generate Ideas
- Intellectual Property
- Life Sciences
- Materials
- Tech Scout
- Unparalleled Data Quality
- Higher Quality Content
- 60% Fewer Hallucinations
Browse by: Latest US Patents, China's latest patents, Technical Efficacy Thesaurus, Application Domain, Technology Topic, Popular Technical Reports.
© 2025 PatSnap. All rights reserved.Legal|Privacy policy|Modern Slavery Act Transparency Statement|Sitemap|About US| Contact US: help@patsnap.com