Compliant manipulator and grabbing operation method thereof
A manipulator and compliant technology, applied in the field of robotics, can solve the problems of control system deviation, affect the compliant control of fruit picking, increase the complexity of the system and control difficulty, and achieve the effect of compliant positioning and simplified system structure
- Summary
- Abstract
- Description
- Claims
- Application Information
AI Technical Summary
Problems solved by technology
Method used
Image
Examples
Embodiment Construction
[0059] In order to make the object, technical solution and advantages of the present invention clearer, the present invention will be described in further detail below in conjunction with specific embodiments and with reference to the accompanying drawings.
[0060] As one of the specific implementations of the present invention, as shown in the figure, a compliant manipulator includes a housing 70, a motion control module A1 is installed inside the housing 70, and the motion control module A1 is electrically connected to a drive unit 10, the drive unit 10 is power-connected with a transmission module 20, the transmission module 20 includes a bottom plate 210, a transmission shaft 300 is installed through the bottom plate 210, and one end of the transmission shaft 300 is power-connected with the drive unit 10 , the transmission shaft 300 is equipped with a torque adjustment bull gear 421 through the bearing C01, the torque adjustment bull gear 421 is meshed with a torque adjust...
PUM
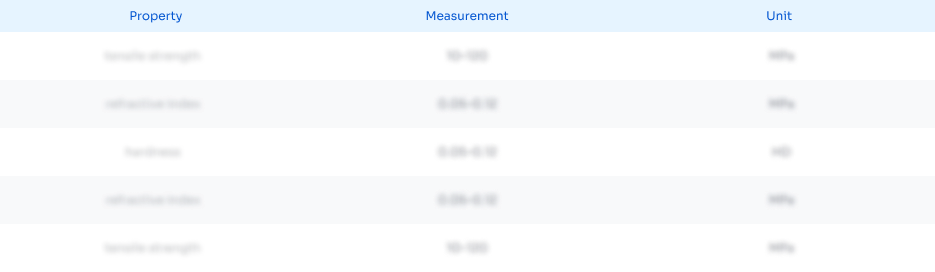
Abstract
Description
Claims
Application Information

- R&D
- Intellectual Property
- Life Sciences
- Materials
- Tech Scout
- Unparalleled Data Quality
- Higher Quality Content
- 60% Fewer Hallucinations
Browse by: Latest US Patents, China's latest patents, Technical Efficacy Thesaurus, Application Domain, Technology Topic, Popular Technical Reports.
© 2025 PatSnap. All rights reserved.Legal|Privacy policy|Modern Slavery Act Transparency Statement|Sitemap|About US| Contact US: help@patsnap.com