Filling control method, device and system
A control method and filling system technology, applied in the field of measurement and control, can solve the problems such as the decline of filling accuracy and the error of the measurement value of the weighing element, and achieve the effect of improving stability and processing accuracy.
- Summary
- Abstract
- Description
- Claims
- Application Information
AI Technical Summary
Problems solved by technology
Method used
Image
Examples
Embodiment 1
[0021] figure 1 It is the flow chart of the filling control method in embodiment one, with reference to figure 1 , the control method includes the steps of:
[0022] S101. Receive a weighing signal from a weighing sensor, and perform a primary filter on the weighing signal to generate a first weighing signal sequence.
[0023] In this step, a primary filter is performed on each sampled weighing signal, and the weighing signal is formed into a weighing signal sequence in chronological order, for example, six weighing signals are sequentially selected to form a weighing signal sequence, and when a new When weighing the signal, the weighing signal is added to the weighing signal sequence, and the weighing signal at the earliest moment in the weighing signal sequence is removed from the sequence to ensure that the length of the sequence remains unchanged.
[0024] Optionally, the first-level filtering in this step includes median filtering, limiting filtering, and Kalman filteri...
Embodiment 2
[0054] figure 2 It is the structural diagram of the filling control device in the second embodiment, refer to figure 2 , the filling control device 100 includes:
[0055] The filter module 1 is configured to receive the weighing signal from the load cell, and perform a primary filter on the weighing signal to generate a first weighing signal sequence. Vibration suppression is performed on the first weighing signal sequence to generate a second weighing signal. Using the second weighing signal to generate a second weighing signal sequence, performing secondary filtering on the second weighing signal sequence to generate a third weighing signal.
[0056] Optionally, the filtering module 1 performing a primary filter on the weighing signal to generate the first weighing signal sequence includes: performing limiting filtering on the sampling sequence of the weighing signal within a unit period to generate the first weighing signal sequence.
[0057] Performing vibration suppr...
Embodiment 3
[0074] image 3 It is a schematic structural diagram of the filling control system in embodiment three, referring to image 3 , this embodiment proposes a filling control system, including the filling control device 100 described in any of the above embodiments, and also includes a filling system 200 and a load cell 300, the filling control device 100, the filling system 200 and the weighing The sensor 300 constitutes a closed-loop control system. Wherein, the filling system 200 is used for generating an initial filling signal and a corrected filling signal. The weighing sensor 300 is used to detect the total weight of the filling container 400 and the current filling, and send a weighing signal to the filling control device 100 . The filling control device 100 sends the difference between the generated third weighing signal and the preset weight signal to the filling system 200, and the filling system 200 uses the difference to generate a filling signal for the next filling...
PUM
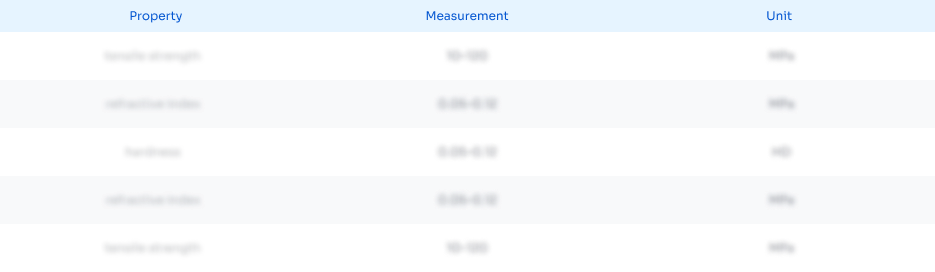
Abstract
Description
Claims
Application Information

- R&D
- Intellectual Property
- Life Sciences
- Materials
- Tech Scout
- Unparalleled Data Quality
- Higher Quality Content
- 60% Fewer Hallucinations
Browse by: Latest US Patents, China's latest patents, Technical Efficacy Thesaurus, Application Domain, Technology Topic, Popular Technical Reports.
© 2025 PatSnap. All rights reserved.Legal|Privacy policy|Modern Slavery Act Transparency Statement|Sitemap|About US| Contact US: help@patsnap.com