Surface processing technology of mineral casting
A technology for mineral castings and surface processing, applied in the field of mineral castings, can solve the problems of insufficient corrosion resistance of mineral castings and cumbersome processes, and achieve the effects of enhanced corrosion resistance, low price and high strength
- Summary
- Abstract
- Description
- Claims
- Application Information
AI Technical Summary
Problems solved by technology
Method used
Image
Examples
Embodiment 1
[0034] The specific steps of the mineral casting surface processing technology are as follows:
[0035] S1. Demoulding on the inner surface of the mold: Drive the high-pressure pump to suck the release agent, pressurize it to 30MPa, and then spray it on the inner surface of the mold for mineral casting casting, so that there is no compressed air in the sprayed release agent to avoid compressed air. Ingress of moisture and other impurities leads to unsatisfactory release effect, which makes the surface of the release agent uneven;
[0036] S2. Coating anti-corrosion coating: mix the raw materials of anti-corrosion coating in equal proportions according to the set amount and put them in the container. The raw materials of anti-corrosion coating include polyacrylate, curing agent, pebbles and river sand, and the anti-corrosion coating The raw materials are: 60kg of polyacrylate, 20kg of curing agent, 12kg of pebbles and 8kg of river sand according to the mass specific gravity, an...
Embodiment 2
[0042] S1. Demoulding on the inner surface of the mold: drive the high-pressure pump to suck the release agent, pressurize it to 15MPa, and then spray it on the inner surface of the mold for casting mineral castings. In this way, there is no compressed air in the sprayed release agent to avoid compressed air. Ingress of moisture and other impurities leads to unsatisfactory release effect, which makes the surface of the release agent uneven;
[0043] S2. Coating anti-corrosion coating: mix the raw materials of anti-corrosion coating in equal proportions according to the set amount and put them in the container. The raw materials of anti-corrosion coating include polyacrylate, curing agent, pebbles and river sand, and the anti-corrosion coating The raw materials are: 5.8kg of polyacrylate, 2.2kg of curing agent, 1.5kg of pebbles and 0.5kg of river sand according to the mass specific gravity, and then use the mechanical arm to paint the anti-corrosion coating evenly on the surface...
PUM
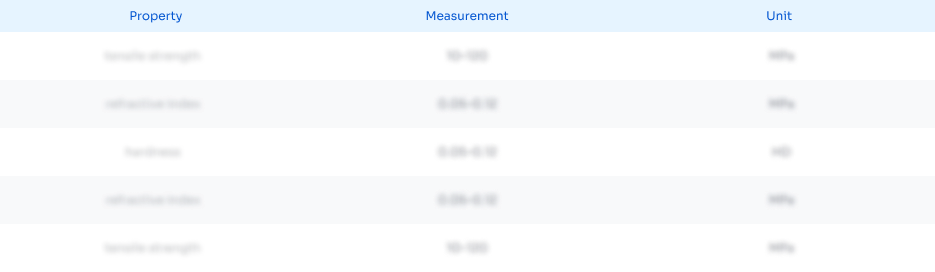
Abstract
Description
Claims
Application Information

- R&D
- Intellectual Property
- Life Sciences
- Materials
- Tech Scout
- Unparalleled Data Quality
- Higher Quality Content
- 60% Fewer Hallucinations
Browse by: Latest US Patents, China's latest patents, Technical Efficacy Thesaurus, Application Domain, Technology Topic, Popular Technical Reports.
© 2025 PatSnap. All rights reserved.Legal|Privacy policy|Modern Slavery Act Transparency Statement|Sitemap|About US| Contact US: help@patsnap.com