Spline structure integrated with multi-stage vibration absorbing function
A secondary vibration reduction and spline technology, applied in transmission parts, belts/chains/gears, mechanical equipment, etc., can reduce vibration and spline tooth percussion, spline percussion abnormal noise, cost increase, etc. problems, to achieve the effect of improving service life, preventing resonance, and being easy to assemble
- Summary
- Abstract
- Description
- Claims
- Application Information
AI Technical Summary
Problems solved by technology
Method used
Image
Examples
Embodiment Construction
[0026] Embodiments of the present invention will be described in detail below in conjunction with the accompanying drawings. The main shock absorber mentioned in this embodiment refers to a component with a shock absorbing function such as a dual-mass flywheel or a shock absorbing driven plate.
[0027] figure 1 A schematic cross-sectional view of the assembly of the present invention is shown; figure 2 A schematic diagram of the damping function of the present invention is shown; image 3 Shows the exploded view of the structure of the present invention; Figure 4 A performance graph of the invention is shown. Such as Figure 1-Figure 4 As shown, the present invention provides a spline structure with integrated multi-stage vibration damping function, including torsion transmission plate 1, main body spline 2, rivet 3, secondary spring 4, primary spring 5, vibration damping spline 6 and The flywheel disc 7 and the torsion transmission plate 1 are used as the input of the...
PUM
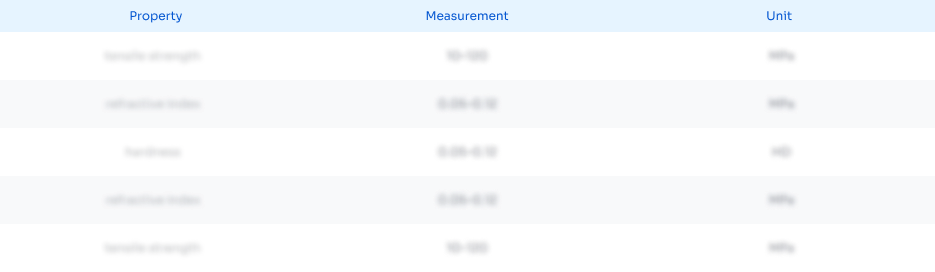
Abstract
Description
Claims
Application Information

- Generate Ideas
- Intellectual Property
- Life Sciences
- Materials
- Tech Scout
- Unparalleled Data Quality
- Higher Quality Content
- 60% Fewer Hallucinations
Browse by: Latest US Patents, China's latest patents, Technical Efficacy Thesaurus, Application Domain, Technology Topic, Popular Technical Reports.
© 2025 PatSnap. All rights reserved.Legal|Privacy policy|Modern Slavery Act Transparency Statement|Sitemap|About US| Contact US: help@patsnap.com