Vacuum glass coating equipment
A technology of vacuum glass and coating equipment, applied in vacuum evaporation coating, sputtering coating, ion implantation coating and other directions, can solve the problems of uneven coating thickness and affecting the quality of glass coating, and achieve good coating quality and use Flexible and convenient effects
- Summary
- Abstract
- Description
- Claims
- Application Information
AI Technical Summary
Problems solved by technology
Method used
Image
Examples
Embodiment 1
[0029] see Figure 1~3 , in an embodiment of the present invention, a vacuum glass coating device includes a support box 1, a support plate 3, a first pressing drum 5, a second pressing drum 6, a transmission roller 7, an electric push rod 8 and a liquid Cylinder 9;
[0030] Wherein, a plurality of said conveying rollers 7 that play a role in transporting and supporting the glass 2 are installed at the bottom of the frame 4, and the said support box 1 is mounted on the left side of the frame 4 in a lifting manner through the electric push rods 8 provided at its four corners. Upper part: an adjustment mechanism for adjusting the relative position between the first compression drum 5 and the second compression drum 6 is installed in the support box 1; the first compression drum 5 is adjusted by the adjustment mechanism The relative position between the second pressing drum 6 can adjust the first pressing drum 5 and the second pressing drum 6 to a suitable distance position acco...
Embodiment 2
[0039] see Figure 1~3 , in an embodiment of the present invention, a vacuum glass coating device includes a support box 1, a support plate 3, a first pressing drum 5, a second pressing drum 6, a transmission roller 7, an electric push rod 8 and a liquid Cylinder 9;
[0040] Wherein, a plurality of said conveying rollers 7 that play a role in transporting and supporting the glass 2 are installed at the bottom of the frame 4, and the said support box 1 is mounted on the left side of the frame 4 in a lifting manner through the electric push rods 8 provided at its four corners. Upper part: an adjustment mechanism for adjusting the relative position between the first compression drum 5 and the second compression drum 6 is installed in the support box 1; the first compression drum 5 is adjusted by the adjustment mechanism The relative position between the second pressing drum 6 can adjust the first pressing drum 5 and the second pressing drum 6 to a suitable distance position acco...
PUM
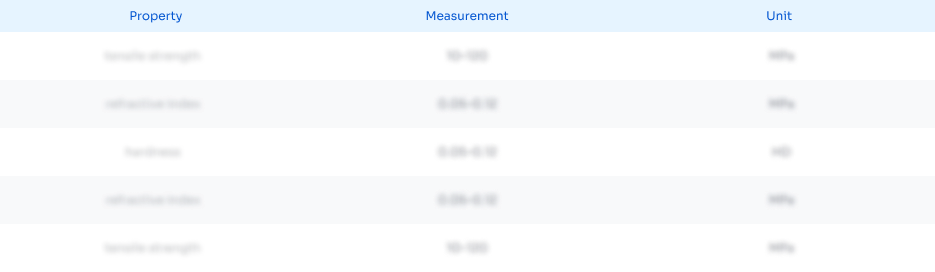
Abstract
Description
Claims
Application Information

- R&D
- Intellectual Property
- Life Sciences
- Materials
- Tech Scout
- Unparalleled Data Quality
- Higher Quality Content
- 60% Fewer Hallucinations
Browse by: Latest US Patents, China's latest patents, Technical Efficacy Thesaurus, Application Domain, Technology Topic, Popular Technical Reports.
© 2025 PatSnap. All rights reserved.Legal|Privacy policy|Modern Slavery Act Transparency Statement|Sitemap|About US| Contact US: help@patsnap.com