Robot pillar structure
A robot and column technology, applied in the field of robots, can solve the problems of dust production and affect the dynamic performance of robots, and achieve the effect of easy maintenance, good rigidity and easy maintenance.
- Summary
- Abstract
- Description
- Claims
- Application Information
AI Technical Summary
Problems solved by technology
Method used
Image
Examples
Embodiment Construction
[0025] The present invention will be described in further detail below in conjunction with the accompanying drawings.
[0026] Such as Figure 1-7 As shown, the present invention includes a base shell 1, a ball screw 2, a sealing intermediate wheel 5, a drive motor 6, a transmission mechanism, a filter and a fan 8, a column frame 10, a slide frame 12, a sealing tape 13, an outer cover 14, and a drag chain 18 and wire nut 19, wherein the base shell 1 is fixedly connected to the bottom of the outer cover 14, and one side surface of the outer cover 14 has a gap along the height direction. The column frame 10 is installed in the outer cover 14, the ball screw 2 is rotatably mounted on the column frame 10, and the lower end is connected with the driving motor 7 installed outside the outer cover 14 through a transmission mechanism. The transmission mechanism of this embodiment includes a driving pulley 6, a synchronous belt 4 and a driven pulley 3, the driving motor 7 is fixed on t...
PUM
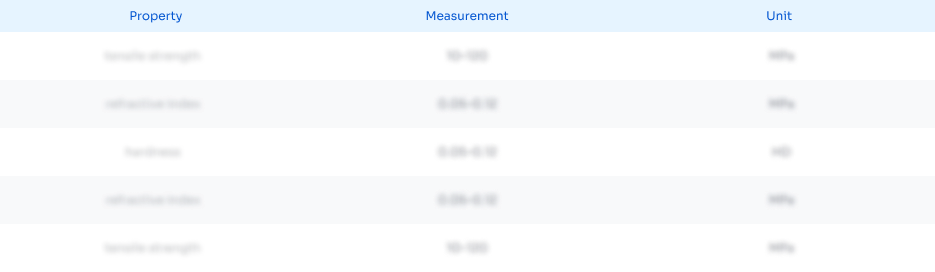
Abstract
Description
Claims
Application Information

- Generate Ideas
- Intellectual Property
- Life Sciences
- Materials
- Tech Scout
- Unparalleled Data Quality
- Higher Quality Content
- 60% Fewer Hallucinations
Browse by: Latest US Patents, China's latest patents, Technical Efficacy Thesaurus, Application Domain, Technology Topic, Popular Technical Reports.
© 2025 PatSnap. All rights reserved.Legal|Privacy policy|Modern Slavery Act Transparency Statement|Sitemap|About US| Contact US: help@patsnap.com