Digital twin modeling method for aero-engine turbine disc-rotor-supporting system
A technology of aero-engine and support system, applied in the direction of electrical digital data processing, special data processing applications, instruments, etc.
- Summary
- Abstract
- Description
- Claims
- Application Information
AI Technical Summary
Problems solved by technology
Method used
Image
Examples
Embodiment Construction
[0033] The present invention will be described in detail below in conjunction with the accompanying drawings.
[0034] The existing modeling methods of the aero-engine turbine disc-rotor-support system are basically based on the optimization of a single physical model, but the aero-engine turbine disc-rotor-support system has been working for a long time under complex conditions coupled with multiple physical fields. Calculation results of physical models will inevitably have inaccuracies. In addition, the existing aeroengine turbine disk-rotor-support system model does not take into account the real-time changes in the working state of the turbine disk-rotor-support system. Since the flight speed, altitude and attitude will change continuously during the flight, the aviation The operating speed, temperature and load of the engine turbine disc-rotor-support system will also change continuously. Using a constant model to simulate the turbine disk-rotor-support system of an aer...
PUM
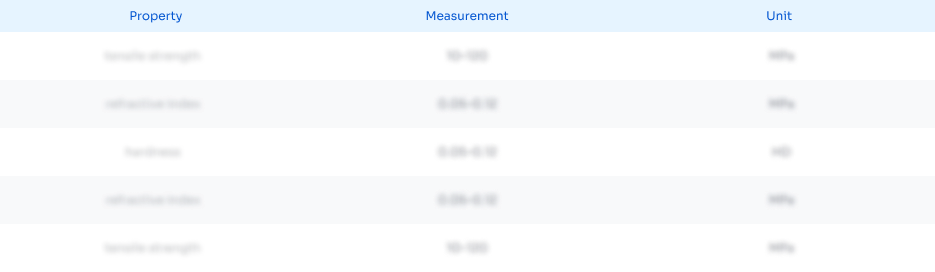
Abstract
Description
Claims
Application Information

- R&D
- Intellectual Property
- Life Sciences
- Materials
- Tech Scout
- Unparalleled Data Quality
- Higher Quality Content
- 60% Fewer Hallucinations
Browse by: Latest US Patents, China's latest patents, Technical Efficacy Thesaurus, Application Domain, Technology Topic, Popular Technical Reports.
© 2025 PatSnap. All rights reserved.Legal|Privacy policy|Modern Slavery Act Transparency Statement|Sitemap|About US| Contact US: help@patsnap.com