Laminated telescopic flat clamp grabbing sliding pipe self-adaptive robot hand device
A robot hand, self-adaptive technology, applied in the directions of manipulators, chucks, manufacturing tools, etc., can solve the problems of uneven grasping force, unstable grasping, affecting application, etc., and achieve large grasping force and automatic grasping force. Harmony and balance, uniform gripping force distribution
- Summary
- Abstract
- Description
- Claims
- Application Information
AI Technical Summary
Problems solved by technology
Method used
Image
Examples
Embodiment Construction
[0031] The specific structure and working principle of the present invention will be further described in detail below in conjunction with the accompanying drawings and embodiments.
[0032] The self-adaptive robot hand device for grabbing sliding pipes with laminated telescopic flat clips designed by the present invention includes a base and N sliding pipe assemblies; the sliding pipe assemblies include guide rods, sliding pipes, spring parts and elastic films; In the slide tube assembly, the slide tube is slidably sleeved on the guide rod, the two ends of the spring member are respectively connected to the guide rod and the slide tube, and the elastic film is sleeved on the slide tube; all the guide rods The centerlines are parallel to each other; there are N through holes on the base; the guide rod passes through the corresponding through holes; it is characterized in that: the self-adaptive robot hand device of the laminated telescopic flat clip grabbing slide tube also inc...
PUM
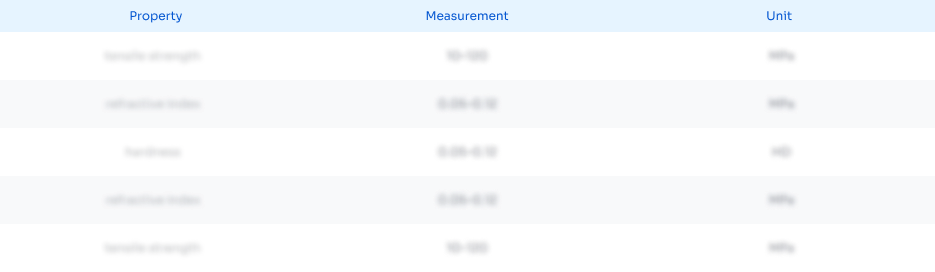
Abstract
Description
Claims
Application Information

- R&D Engineer
- R&D Manager
- IP Professional
- Industry Leading Data Capabilities
- Powerful AI technology
- Patent DNA Extraction
Browse by: Latest US Patents, China's latest patents, Technical Efficacy Thesaurus, Application Domain, Technology Topic, Popular Technical Reports.
© 2024 PatSnap. All rights reserved.Legal|Privacy policy|Modern Slavery Act Transparency Statement|Sitemap|About US| Contact US: help@patsnap.com