Three-column two-membrane coupled reinforced refining method for fuel ethanol
A technology for fuel ethanol and ethanol vapor, which is applied in chemical instruments and methods, preparation of hydroxyl compounds, preparation of organic compounds, etc., can solve the problems of poor compatibility of materials and heat in the rectification section and purification section, and achieve high-efficiency and low-energy consumption preparation , save steam, simple operation effect
- Summary
- Abstract
- Description
- Claims
- Application Information
AI Technical Summary
Problems solved by technology
Method used
Image
Examples
Embodiment 1
[0042] The process flow diagram is figure 1 Said, the raw material of the fermentation mash is corn, and the temperature is 29.9°C. Fixed vacuum distillation column 1 and pressurized distillation column 2 have a plate number of 57, fixed pressurized distillation column 3 has a plate number of 61, and the feed positions of columns 1, 2 and 3 are at 35, 35 and 45 plates respectively. (counting from the tower kettle). The reflux ratio of the fixed column 1 is 1.2, the reflux ratio of the fixed pressure rectification column 2 is 1.8, and the reflux ratio of the fixed pressure rectification column 3 is 1.4. The ethanol volume concentration of the fermented mash is 5.4%. After feeding, the operating conditions of each tower in the combined tower, the amount of steam consumed by the system per unit of fuel ethanol, the energy saving situation compared with the traditional process, and the energy saving situation relative to the combined tower molecular sieve integrated process As s...
Embodiment 2
[0044] The process flow diagram is figure 1 Said, the raw material of the fermentation mash is corn, and the temperature is 29.9°C. Fixed vacuum distillation column 1 and pressurized distillation column 2 have a plate number of 57, fixed pressurized distillation column 3 has a plate number of 61, and the feed positions of columns 1, 2 and 3 are at 35, 35 and 45 plates respectively. (counting from the tower kettle). The reflux ratio of the fixed column 1 is 1.2, the reflux ratio of the fixed pressure rectification column 2 is 1.8, and the reflux ratio of the fixed pressure rectification column 3 is 1.4. The ethanol volume concentration of the fermented mash is 11.8%. After feeding, the operating conditions of each tower in the combined tower, the amount of steam consumed by the system per unit of fuel ethanol, the energy saving situation compared with the traditional process, and the energy saving situation relative to the molecular sieve integrated process of the combined tow...
Embodiment 3
[0046] The process flow diagram is figure 1 Said, the raw material of the fermentation mash is corn, and the temperature is 29.9°C. Fixed vacuum distillation column 1 and pressurized distillation column 2 have a plate number of 57, fixed pressurized distillation column 3 has a plate number of 61, and the feed positions of columns 1, 2 and 3 are at 35, 35 and 45 plates respectively. (counting from the tower kettle). The reflux ratio of the fixed vacuum distillation column 1 is 1.2, the reflux ratio of the fixed vacuum distillation column 2 is 1.8, and the reflux ratio of the fixed vacuum distillation column 3 is 1.4. The ethanol volume concentration of the fermented mash is 13.6%. After feeding, the operating conditions of each tower in the combined tower, the amount of steam consumed by the system per unit of fuel ethanol, the energy saving situation compared with the traditional process, and the energy saving situation relative to the combined tower molecular sieve integrate...
PUM
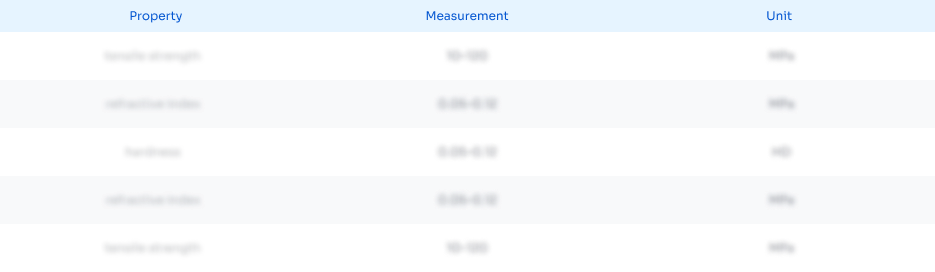
Abstract
Description
Claims
Application Information

- Generate Ideas
- Intellectual Property
- Life Sciences
- Materials
- Tech Scout
- Unparalleled Data Quality
- Higher Quality Content
- 60% Fewer Hallucinations
Browse by: Latest US Patents, China's latest patents, Technical Efficacy Thesaurus, Application Domain, Technology Topic, Popular Technical Reports.
© 2025 PatSnap. All rights reserved.Legal|Privacy policy|Modern Slavery Act Transparency Statement|Sitemap|About US| Contact US: help@patsnap.com