Finish machining process of plastic processing molded metal part
A metal forming and plastic processing technology, applied in spraying devices, coatings, liquid spraying devices, etc., can solve the problems of inconsistent coating thickness, poor spraying effect, uneven coating, etc., to ensure uniformity, avoid low efficiency, good effect
- Summary
- Abstract
- Description
- Claims
- Application Information
AI Technical Summary
Problems solved by technology
Method used
Image
Examples
Embodiment Construction
[0038] The embodiments of the present invention will be described in detail below with reference to the accompanying drawings, but the present invention can be implemented in a variety of different ways defined and covered by the claims.
[0039] Such as Figure 1 to Figure 6 As shown, a finishing process of plastic forming metal parts includes the following steps:
[0040] S1. Grinding: Grinding of defects such as burrs on the surface of metal parts through a grinding wheel;
[0041] S2. Surface cleaning: Manually clean the remaining dust, iron filings and other impurities on the metal parts polished in step S1;
[0042] S3. Spraying treatment: the metal parts cleaned in step S2 are placed on the conveyor belt 2 for transportation, and the spraying device 3 sprays the outer surface of the metal parts;
[0043] S4. Drying: Send the sprayed metal parts to the shelf to dry naturally;
[0044] S5. Film-coated packaging: Film-coated packaging of metal parts after drying;
[0045] S6. Palleti...
PUM
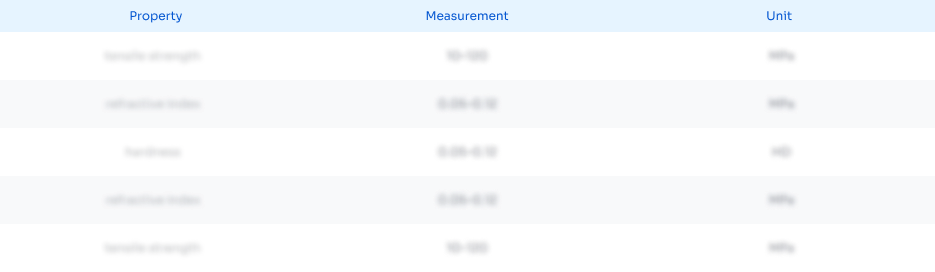
Abstract
Description
Claims
Application Information

- R&D
- Intellectual Property
- Life Sciences
- Materials
- Tech Scout
- Unparalleled Data Quality
- Higher Quality Content
- 60% Fewer Hallucinations
Browse by: Latest US Patents, China's latest patents, Technical Efficacy Thesaurus, Application Domain, Technology Topic, Popular Technical Reports.
© 2025 PatSnap. All rights reserved.Legal|Privacy policy|Modern Slavery Act Transparency Statement|Sitemap|About US| Contact US: help@patsnap.com