Mechanical arm calibration system and calibration method based on four-eye stereo vision
A technology of stereo vision and calibration system, which is applied to manipulators, program-controlled manipulators, manufacturing tools, etc., can solve the problems of time-consuming, low positioning accuracy of manipulators, and expensive measurement equipment, and achieves low cost and easy operation. Effect
- Summary
- Abstract
- Description
- Claims
- Application Information
AI Technical Summary
Problems solved by technology
Method used
Image
Examples
Embodiment Construction
[0044] The present invention will be further described in detail below in conjunction with the accompanying drawings and embodiments, so that those skilled in the art can implement it with reference to the description.
[0045] like Figure 1~2 As shown, the present invention provides a robotic arm calibration system based on four-eye stereo vision, comprising a robotic arm 1, a control box 2, and a computer 3, the control box 2 is connected to the computer 3, and the control box 2 controls the The motion of mechanical arm 1 also includes:
[0046] Two binocular cameras 4, two binocular cameras 4 are respectively distributed in the front and side of the mechanical arm 1, the binocular cameras 4 are connected with the computer 3, and the binocular cameras 4 are fixed on the computer in real time. The mechanical arm 1 takes pictures, and transmits the image data to the computer 3, and the software in the computer 3 recognizes the marking points 5 on the captured mechanical arm ...
PUM
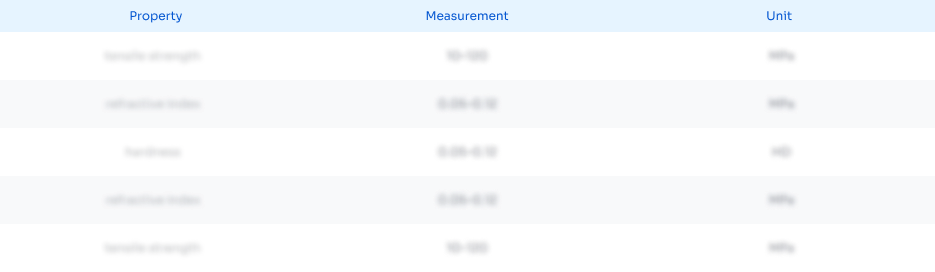
Abstract
Description
Claims
Application Information

- R&D
- Intellectual Property
- Life Sciences
- Materials
- Tech Scout
- Unparalleled Data Quality
- Higher Quality Content
- 60% Fewer Hallucinations
Browse by: Latest US Patents, China's latest patents, Technical Efficacy Thesaurus, Application Domain, Technology Topic, Popular Technical Reports.
© 2025 PatSnap. All rights reserved.Legal|Privacy policy|Modern Slavery Act Transparency Statement|Sitemap|About US| Contact US: help@patsnap.com