Closed-loop control-based micro-Newton order micro-thrust dynamic test table and test method
A closed-loop control and dynamic testing technology, applied in the field of physical mechanics, can solve problems such as micro-new level thrust dynamic testing cannot be achieved, and achieve the effects of improving testing capabilities, suppressing the influence of external noise, and increasing response frequency
- Summary
- Abstract
- Description
- Claims
- Application Information
AI Technical Summary
Problems solved by technology
Method used
Image
Examples
Embodiment Construction
[0045] In order to make the object, technical solution and advantages of the present invention clearer, the embodiments disclosed in the present invention will be further described in detail below in conjunction with the accompanying drawings.
[0046] In this embodiment, the closed-loop control-based micro-neutral-level micro-thrust dynamic test bench includes: a swing arm 1, a calibration coil 2, a calibration magnet 3, a calibration controller 4, a displacement sensor 5, a displacement sensor clip 6, PID closed-loop control module 7 , displacement meter controller 8 , damping mechanism 9 , driving force coil 10 , flexible shaft mechanism 11 and base 12 .
[0047] Such as figure 1 and figure 2 , the swing arm 1 is installed on the base 12 through the flexible shaft mechanism 11 . The calibration coil 2 is wound outside the calibration magnet 3 and connected with the calibration controller 4 . The driving force coil 10 , the displacement gauge controller 8 and the calibra...
PUM
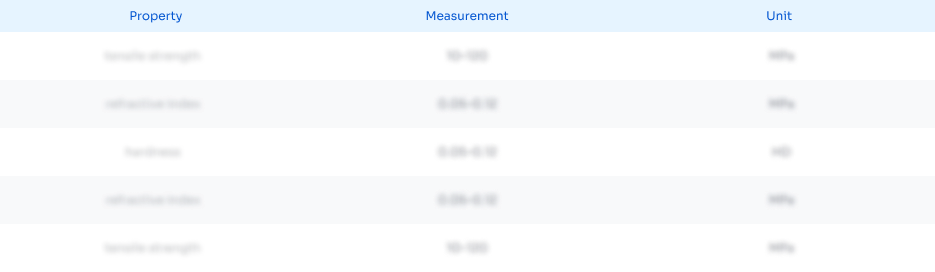
Abstract
Description
Claims
Application Information

- R&D
- Intellectual Property
- Life Sciences
- Materials
- Tech Scout
- Unparalleled Data Quality
- Higher Quality Content
- 60% Fewer Hallucinations
Browse by: Latest US Patents, China's latest patents, Technical Efficacy Thesaurus, Application Domain, Technology Topic, Popular Technical Reports.
© 2025 PatSnap. All rights reserved.Legal|Privacy policy|Modern Slavery Act Transparency Statement|Sitemap|About US| Contact US: help@patsnap.com