Grate closed-die forging technology and forming closed die
A grating bar closed-type, die forging technology, applied in the field of sintering forging, can solve the problems of harsh working conditions of grate bars, increase of grate bars, wearing parts, etc., and achieve the effect of improving product quality and production efficiency and reducing material costs
- Summary
- Abstract
- Description
- Claims
- Application Information
AI Technical Summary
Problems solved by technology
Method used
Image
Examples
Embodiment 1
[0051] like figure 1 As shown, the embodiment of the present invention provides a kind of grate bar closed die forging process, comprises steps:
[0052] Step S100, blanking, selecting a bar according to the total length and projected area of the forging blank;
[0053] The specific steps of bar calculation are as follows:
[0054] Step 101, making a three-dimensional graphic through UG according to the forging blank, and calculating the quality of the bar according to the three-dimensional image;
[0055] Step 102. Determine the length of the bar according to the cavity, and calculate the diameter of the bar according to the length and mass of the bar. The specific calculation process is:
[0056] m=ρV, V=πD 2 L / 4,
[0057] get: Among them, m is the quality of the blank, ρ is the density of the blank, V is the volume of the blank, D is the diameter of the bar, and L is the length of the blank;
[0058] Step 103. On the premise of determining the blanking length, enla...
Embodiment 2
[0097] like Figure 1 to Figure 4 Shown, a kind of grate bar forming closed mold, comprises the upper die cover 1 that connects patrix and the lower die cover 5 that connects lower mold, and die 4 and convex film 3, is installed on the upper die cover 1 and is used for connecting upper die cover 1. The die set 1 and the fixing plate 2 of the punch 3 are used to connect the punch 3 and the upper die set 1. The punch 3 and the die 4 are generally made of H13 die steel. The plate connection can reduce the use of forming die materials and save the manufacturing cost of the whole set of dies.
[0098] And by setting the elastic pad 10 between the punch 3 and the fixed plate 2, a certain elastic buffer can be provided during the stamping process. The elastic pad 10 adopts a sheet-shaped structure made of H13 die steel material, and the sheet The cross-section of the shaped structure is arc-shaped, and the elastic structure formed by the superposition of several arcs, or the superim...
PUM
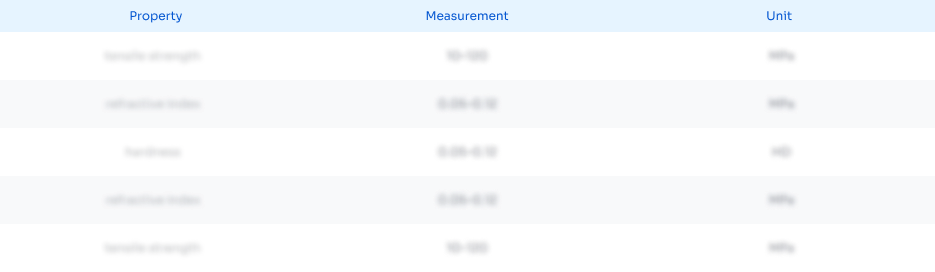
Abstract
Description
Claims
Application Information

- R&D
- Intellectual Property
- Life Sciences
- Materials
- Tech Scout
- Unparalleled Data Quality
- Higher Quality Content
- 60% Fewer Hallucinations
Browse by: Latest US Patents, China's latest patents, Technical Efficacy Thesaurus, Application Domain, Technology Topic, Popular Technical Reports.
© 2025 PatSnap. All rights reserved.Legal|Privacy policy|Modern Slavery Act Transparency Statement|Sitemap|About US| Contact US: help@patsnap.com