Telescopic structure of crane
A telescopic and crane technology, which is applied in the direction of cranes, walking bridge cranes, load hanging components, etc., can solve the problems of crane running track interference, poor adjustment performance of handling work, and affecting the stable movement of telescopic beams, etc., to achieve improved stability sexual effect
- Summary
- Abstract
- Description
- Claims
- Application Information
AI Technical Summary
Problems solved by technology
Method used
Image
Examples
Embodiment Construction
[0029] like Figure 1 to Figure 4 Telescoping structure of the crane shown, including
[0030] Column 1, set on the ground;
[0031] The steel beam 2 is connected to the top of the column 1;
[0032] The first guide rail 3 is symmetrically arranged on the bottom of the steel beam 2;
[0033] The first drive wheel 4 is arranged on the first guide rail 3;
[0034] The balance beam 6 is arranged directly under the steel beam 2, and is connected to the first driving wheel 4 through the first connecting frame 9;
[0035] The second guide rail 7 is arranged at the lower end of the balance beam 6;
[0036] The second driving wheel 8 is arranged on the second guide rail 7;
[0037] The telescopic beam 10 is arranged below the balance beam 6 and is connected to the second driving wheel 8 through the second connecting frame,
[0038] The third guide rail 11 is arranged at the lower end of the telescopic beam 10;
[0039] The hoisting device is arranged on the third guide rail 11;...
PUM
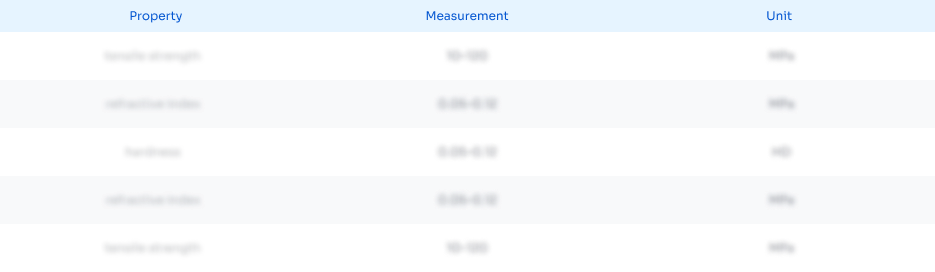
Abstract
Description
Claims
Application Information

- Generate Ideas
- Intellectual Property
- Life Sciences
- Materials
- Tech Scout
- Unparalleled Data Quality
- Higher Quality Content
- 60% Fewer Hallucinations
Browse by: Latest US Patents, China's latest patents, Technical Efficacy Thesaurus, Application Domain, Technology Topic, Popular Technical Reports.
© 2025 PatSnap. All rights reserved.Legal|Privacy policy|Modern Slavery Act Transparency Statement|Sitemap|About US| Contact US: help@patsnap.com