Calibration method for circular grating eccentricity parameters of a flexible arm coordinate measuring machine
A coordinate measuring machine and parameter calibration technology, which is applied in the field of precision measurement, can solve problems such as difficult on-site operation, and achieve the effects of convenient operation, high calibration efficiency, and fast convergence speed
- Summary
- Abstract
- Description
- Claims
- Application Information
AI Technical Summary
Problems solved by technology
Method used
Image
Examples
Embodiment Construction
[0060]The present invention will be further explained below in conjunction with the embodiments and the drawings of the specification.
[0061]The method for calibrating the circular grating eccentricity parameters of the flexible arm coordinate measuring machine of the present invention is aimed at the research object. The structure of the flexible arm coordinate measuring machine is as followsfigure 1 As shown, the flexible arm coordinate measuring machine is composed of a base 1, a fixed arm 2, a measuring arm 3, a rotating joint 4 and a probe 5. The flexible arm coordinate measuring machine has 6 degrees of freedom, of which 6 degrees of freedom Corresponding to 6 rotary joints, each joint is equipped with a circular grating angle sensor. Since the sensor has eccentricity errors due to processing and assembly during the manufacturing process, it is necessary to calibrate each circular grating sensor during use. The method of the present invention includes the following steps:
[0062]...
PUM
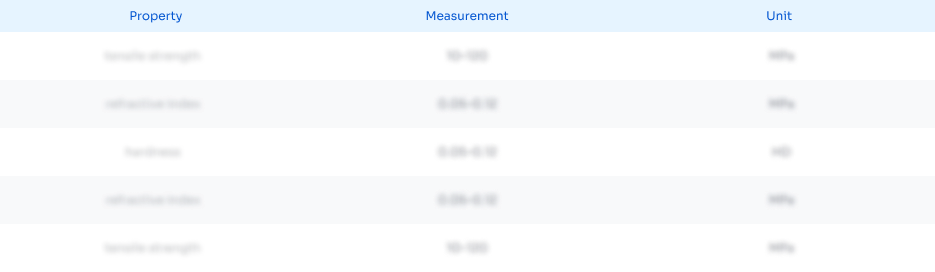
Abstract
Description
Claims
Application Information

- R&D
- Intellectual Property
- Life Sciences
- Materials
- Tech Scout
- Unparalleled Data Quality
- Higher Quality Content
- 60% Fewer Hallucinations
Browse by: Latest US Patents, China's latest patents, Technical Efficacy Thesaurus, Application Domain, Technology Topic, Popular Technical Reports.
© 2025 PatSnap. All rights reserved.Legal|Privacy policy|Modern Slavery Act Transparency Statement|Sitemap|About US| Contact US: help@patsnap.com