A variable-angle two-dimensional ultrasonic vibration assisted machining platform based on flexible hinges
A two-dimensional ultrasonic vibration and flexible hinge technology, applied in the direction of fluid using vibration, can solve problems such as difficulty, high cost of transformation, and complicated design and development process, and achieve the effects of avoiding transformation, high precision and efficiency
- Summary
- Abstract
- Description
- Claims
- Application Information
AI Technical Summary
Problems solved by technology
Method used
Image
Examples
Embodiment Construction
[0022] The present invention will be further described in detail below in conjunction with the accompanying drawings and embodiments.
[0023] Such as Figure 1 to Figure 4 As shown, a variable-angle two-dimensional ultrasonic vibration auxiliary processing platform based on flexible hinges includes a rectangular bottom plate 1 and a vibrating block 3. The bottom plate 1 cooperates with the seat ring of the thrust bearing 11 through an annular platform provided on its upper surface. The vibrating block 3 cooperates with the shaft ring of the thrust bearing 11 through the circular boss provided on its lower surface, so as to realize the Z-direction support for the vibrating block 3, and at the same time, because the reasoning bearing does not limit the axial displacement, it can realize two-dimensional Ultrasonic vibration, the upper surface of the bottom plate 1 is provided with four flange seats 7 along the circumference, and the first ultrasonic vibrator 5 and the second ult...
PUM
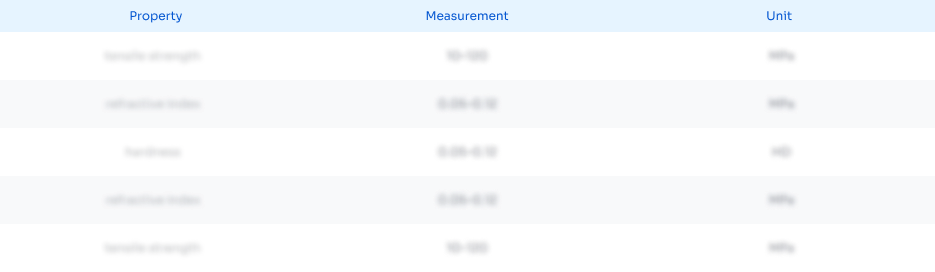
Abstract
Description
Claims
Application Information

- R&D
- Intellectual Property
- Life Sciences
- Materials
- Tech Scout
- Unparalleled Data Quality
- Higher Quality Content
- 60% Fewer Hallucinations
Browse by: Latest US Patents, China's latest patents, Technical Efficacy Thesaurus, Application Domain, Technology Topic, Popular Technical Reports.
© 2025 PatSnap. All rights reserved.Legal|Privacy policy|Modern Slavery Act Transparency Statement|Sitemap|About US| Contact US: help@patsnap.com