Method for repairing aviation weak-rigidity casing
A technology of weak rigidity and casing, applied in the field of aviation slender thin-walled weak rigid casing repair, can solve the problems of long repair cycle, less machining allowance, no regularity, etc., to shorten the repair cycle and improve the alignment accuracy. , Guarantee the effect of qualified rate
- Summary
- Abstract
- Description
- Claims
- Application Information
AI Technical Summary
Problems solved by technology
Method used
Image
Examples
Embodiment Construction
[0023] Below in conjunction with accompanying drawing and embodiment the present invention will be further described:
[0024] In order to describe this process in detail, a certain type of shell is taken as an example. The shell is composed of a main shell 1845 and other four small shells 1846, 1847, 1848, and 1849. The shafting distribution is as follows: figure 1 shown. Among them, the spacing error of each shaft system is 0.06, the parallelism between the shaft systems is 0.03 / 100, the runout requirement between the holes in the shaft system is 0.04, the geometric length is 1072, the arc expansion length reaches 1400, and the wall thickness The thinnest part is only 5.5, and the material is cast magnesium alloy, which is a typical slender, thin-walled and weakly rigid shell part.
[0025] Parts analysis and preparatory work before repair:
[0026] 1. The shell, of which 1845 is the main shell, is the priority to keep the parts.
[0027] 2. Check the shell before repairi...
PUM
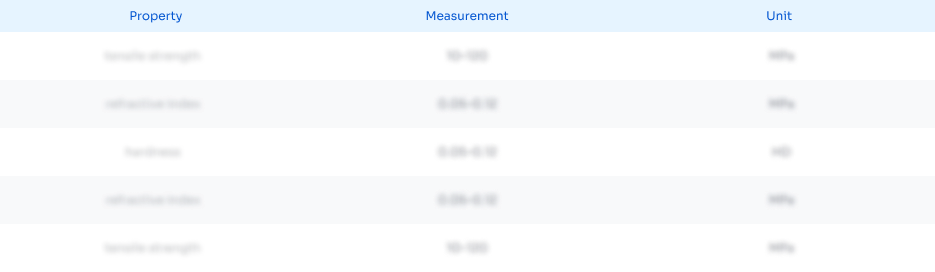
Abstract
Description
Claims
Application Information

- Generate Ideas
- Intellectual Property
- Life Sciences
- Materials
- Tech Scout
- Unparalleled Data Quality
- Higher Quality Content
- 60% Fewer Hallucinations
Browse by: Latest US Patents, China's latest patents, Technical Efficacy Thesaurus, Application Domain, Technology Topic, Popular Technical Reports.
© 2025 PatSnap. All rights reserved.Legal|Privacy policy|Modern Slavery Act Transparency Statement|Sitemap|About US| Contact US: help@patsnap.com