Backstepping sliding mode maximum wave energy capture method
A backstepping sliding mode and backstepping technology, which is applied in the control of generators, electronic commutation motor control, control systems, etc., can solve the problem of inability to track linear generators in real time with wave vertical speed, unsatisfactory development, and wave frequency amplitude. instability, etc.
- Summary
- Abstract
- Description
- Claims
- Application Information
AI Technical Summary
Problems solved by technology
Method used
Image
Examples
Embodiment 1
[0290] The structure diagram of the direct drive wave energy conversion device provided by this embodiment is as follows Figure 11 shown. A key feature of direct drive wave energy conversion systems is the use of permanent magnet linear motors as generators compared to wave energy conversion using hydraulic or pneumatic systems. During the working process, the mover of the PMLG is directly connected to the buoy or buoy through the direct contact of the buoy or buoy with the wave. As the waves rise and fall, the waves convert mechanical energy into mechanical energy for the buoy.
Embodiment 2
[0292] This embodiment provides the working flow diagram of the direct-drive wave energy generation system, such as Figure 12 As shown, under the action of waves, the mover of the generator drives the generator to generate electricity through the reciprocating linear motion of the float. The required AC output of the generator is controlled by a rectifier and a controller to obtain the best output effect, and then the output electric energy is stored to an energy storage device or a power supply device for power supply. The controller generates control signals according to real-time wave height and wave frequency and generator output. The SVPWM generator controls the switch to start and stop the rectifier in real time, and adjust the load of the waveform energy power generation system in real time. Electromagnetic force and reference current. The frequency of ocean waves The frequency of the incident waves of the wave energy generation system is consistent, and the entire s...
Embodiment 3
[0294] This embodiment provides a backstepping sliding mode maximum power tracking system control framework, such as Figure 13 As shown, a control strategy for PMLG speed control is proposed. By tracking the dq axis current components, the BSMC controller is designed to stabilize the current error to obtain the input v. The pulse generator voltage pulse width modulation (SVPWM) voltage signal is then sent out through it. The pulse adjusts the working state of the converter on the machine side. It can be seen that as long as the dq-axis current generator can track the input reference current in real time, the anti-electromagnetic force of the generator can be adjusted online in real time to approach the reference value. It can ensure that the energy conversion system (PMLG) and the wave reach resonance and obtain the maximum wave energy.
[0295] The serial numbers of the above embodiments of the present invention are for description only, and do not represent the advantage...
PUM
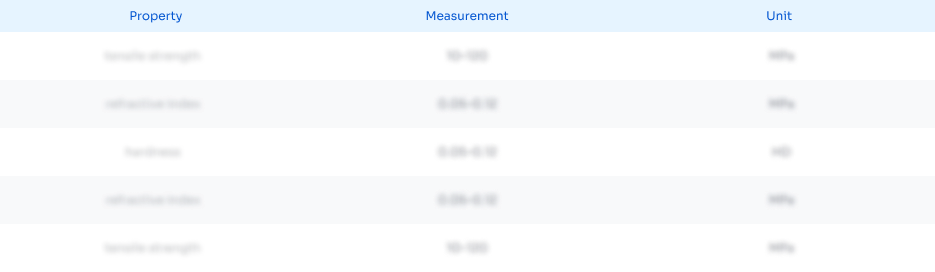
Abstract
Description
Claims
Application Information

- R&D Engineer
- R&D Manager
- IP Professional
- Industry Leading Data Capabilities
- Powerful AI technology
- Patent DNA Extraction
Browse by: Latest US Patents, China's latest patents, Technical Efficacy Thesaurus, Application Domain, Technology Topic, Popular Technical Reports.
© 2024 PatSnap. All rights reserved.Legal|Privacy policy|Modern Slavery Act Transparency Statement|Sitemap|About US| Contact US: help@patsnap.com