Modular friction and wear testing machine and testing method thereof
A friction and wear test, modular technology, applied in the direction of testing wear resistance, measuring devices, instruments, etc., can solve the problems of easy disassembly and cleaning of internal parts, adverse effects on experimental accuracy, single use function, etc., to reduce vibration interference , reducing the impact of results, the effect of functional diversification
- Summary
- Abstract
- Description
- Claims
- Application Information
AI Technical Summary
Problems solved by technology
Method used
Image
Examples
Embodiment 1
[0027] Embodiment 1: as Figure 1-Figure 6 As shown, a modular friction and wear testing machine includes a housing, a friction disc 28, a sample holding device, a loading device, a pressure sensor 6, a wireless torque sensor 3 and a stepping motor 2, and a loading device is installed on the left side of the housing. device, the inner end of the loading device is connected to the sample clamping device, a stepping motor 2 is installed on the left side of the housing, the motor shaft of the stepping motor 2 is connected to the transmission shaft 4 through the wireless torque sensor 3, and the transmission shaft 4 is axially movable In the blind hole on the connection friction disc 28, the friction disc 28 faces the sample clamping device, the pressure sensor 6 is installed on the inner end of the transmission shaft 4 and leans against the blind hole, and the end surface of the friction disc 28 facing the direction of the sample is installed with a protruding A plurality of even...
Embodiment 2
[0036] Embodiment 2: A test method of a modular friction and wear testing machine, the method is: first check whether the parts of each part are complete, and then install the sample on the sample clamping device to ensure reliable clamping, and install four Positioning rod and loading stud, and install a large spring on the loading stud, install the entire sample clamping device on the transparent shell 1 on the left, and pre-tighten it with the lock nut outside the shell 1, and then fine-tune it The fine-tuning nut in the mechanism carries out the positive position of the sample, and the external observation adjusts it to be vertical, and then the friction disc equipped with the pressure sensor is connected to the motor shaft of the stepping motor through the transmission shaft equipped with the wireless torque sensor, and then the electrochemical The temperature access point of the workstation is connected to the temperature sensor, and then the working electrode and the aux...
PUM
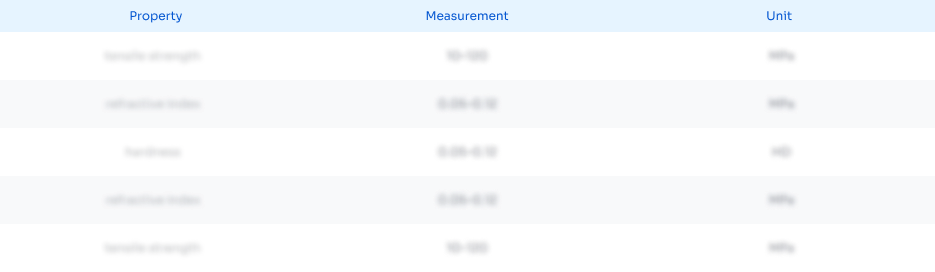
Abstract
Description
Claims
Application Information

- R&D
- Intellectual Property
- Life Sciences
- Materials
- Tech Scout
- Unparalleled Data Quality
- Higher Quality Content
- 60% Fewer Hallucinations
Browse by: Latest US Patents, China's latest patents, Technical Efficacy Thesaurus, Application Domain, Technology Topic, Popular Technical Reports.
© 2025 PatSnap. All rights reserved.Legal|Privacy policy|Modern Slavery Act Transparency Statement|Sitemap|About US| Contact US: help@patsnap.com