Vibration isolator with high static low dynamic stiffness characteristics and rail system with vibration isolator
A technology of low dynamic stiffness and vibration isolators, which is applied in the field of rail vibration and noise reduction, can solve the problems of increased static deformation, narrow vibration isolation frequency range of vibration isolators, and poor low frequency vibration reduction effect, so as to reduce low frequency Vibration transmission, improving the frequency range of vibration isolation, and isolating the effect of low frequency vibration
- Summary
- Abstract
- Description
- Claims
- Application Information
AI Technical Summary
Problems solved by technology
Method used
Image
Examples
Embodiment Construction
[0030] The following will clearly and completely describe the technical solutions in the embodiments of the present invention with reference to the drawings in the embodiments of the present invention. Apparently, the described embodiments are only some of the embodiments of the present invention, but not all of them. The following description of at least one exemplary embodiment is merely illustrative in nature and in no way taken as limiting the invention, its application or uses. Based on the embodiments of the present invention, all other embodiments obtained by persons of ordinary skill in the art without creative efforts fall within the protection scope of the present invention.
[0031] Such as Figure 1 to Figure 3 As shown, Embodiment 1 of the present invention provides a vibration isolator with high static and low dynamic stiffness characteristics, including: a positive stiffness assembly 10, the positive stiffness assembly 10 includes a base 11 and a first elastic...
PUM
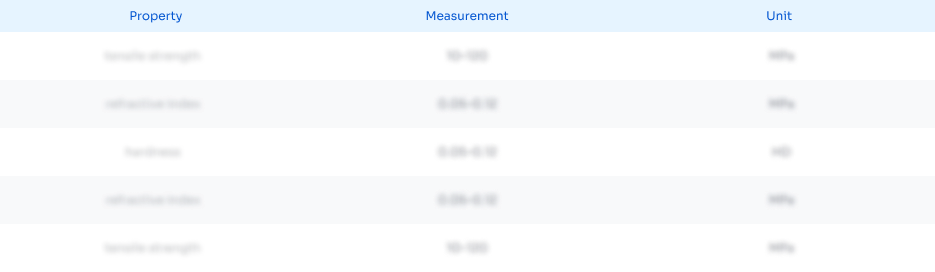
Abstract
Description
Claims
Application Information

- R&D
- Intellectual Property
- Life Sciences
- Materials
- Tech Scout
- Unparalleled Data Quality
- Higher Quality Content
- 60% Fewer Hallucinations
Browse by: Latest US Patents, China's latest patents, Technical Efficacy Thesaurus, Application Domain, Technology Topic, Popular Technical Reports.
© 2025 PatSnap. All rights reserved.Legal|Privacy policy|Modern Slavery Act Transparency Statement|Sitemap|About US| Contact US: help@patsnap.com