Wood-plastic composite floor and preparation method thereof
A technology of composite flooring and plastic wood, which is applied in the field of flooring, can solve the problems of short service life, poor wear resistance and scratch resistance, and achieve good wear resistance, good scratch resistance and increased strength.
- Summary
- Abstract
- Description
- Claims
- Application Information
AI Technical Summary
Problems solved by technology
Method used
Image
Examples
Embodiment 1
[0041] This embodiment proposes a plastic-wood composite floor, including the following raw materials in parts by weight: 30 parts of PVC resin, 40 parts of wood powder, 5 parts of adhesive, 5 parts of modifier, 6 parts of plasticizer, and flame retardant 7 parts, 15 parts of composite fiber, 15 parts of polyester fiber, 20 parts of bamboo charcoal fiber, 20 parts of carbon rubber, 7 parts of hollow microspheres, 8 parts of polytetrafluoroethylene, 11 parts of wear-resistant rubber, 9 parts of polypropylene fiber, 5 parts of glass powder, 10 parts of ceramic powder, 10 parts of wax powder, 15 parts of epoxy resin, and 5 parts of silicone resin.
[0042] Its preparation method comprises the following steps:
[0043] S1: Put PVC resin, wood powder, adhesive, modifier, plasticizer, flame retardant, and composite fiber into the stirring equipment for stirring and mixing. The speed of the stirring equipment is 700r / min, and the stirring time is 45min. Uniformly obtain the first mi...
Embodiment 2
[0048] This embodiment proposes a plastic-wood composite floor, including the following raw materials in parts by weight: 34 parts of PVC resin, 41 parts of wood powder, 6 parts of adhesive, 6 parts of modifier, 7 parts of plasticizer, and flame retardant 8 parts, 16 parts of composite fiber, 17 parts of polyester fiber, 21 parts of bamboo charcoal fiber, 21 parts of carbon rubber, 8 parts of hollow microspheres, 9 parts of polytetrafluoroethylene, 12 parts of wear-resistant rubber, 10 parts of polypropylene fiber, 6 parts of glass powder, 11 parts of ceramic powder, 11 parts of wax powder, 16 parts of epoxy resin, and 6 parts of silicone resin.
[0049] Its preparation method comprises the following steps:
[0050] S1: Put PVC resin, wood powder, adhesive, modifier, plasticizer, flame retardant, and composite fiber into the mixing equipment for mixing. The speed of the mixing equipment is 720r / min, and the mixing time is 47min. Uniformly obtain the first mixture;
[0051] S...
Embodiment 3
[0055] This embodiment proposes a plastic-wood composite floor, including the following raw materials in parts by weight: 38 parts of PVC resin, 42 parts of wood powder, 7 parts of adhesive, 7 parts of modifier, 8 parts of plasticizer, and flame retardant 9 parts, 17 parts of composite fiber, 19 parts of polyester fiber, 22 parts of bamboo charcoal fiber, 22 parts of carbon rubber, 9 parts of hollow microspheres, 10 parts of polytetrafluoroethylene, 13 parts of wear-resistant rubber, 11 parts of polypropylene fiber, 7 parts of glass powder, 12 parts of ceramic powder, 12 parts of wax powder, 17 parts of epoxy resin, and 7 parts of silicone resin.
[0056] Its preparation method comprises the following steps:
[0057] S1: Put PVC resin, wood powder, adhesive, modifier, plasticizer, flame retardant, and composite fiber into the stirring equipment for stirring and mixing. The speed of the stirring equipment is 740r / min, and the stirring time is 49min. Uniformly obtain the first ...
PUM
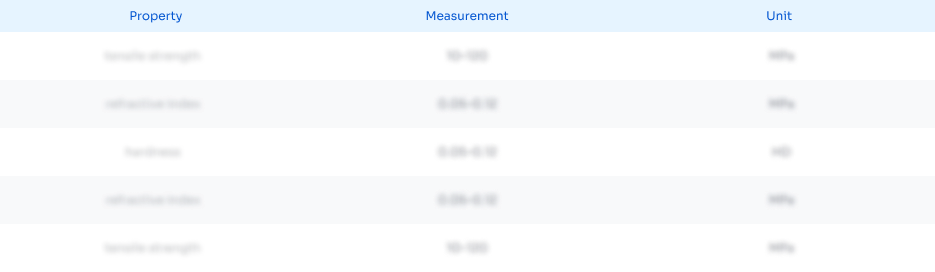
Abstract
Description
Claims
Application Information

- R&D Engineer
- R&D Manager
- IP Professional
- Industry Leading Data Capabilities
- Powerful AI technology
- Patent DNA Extraction
Browse by: Latest US Patents, China's latest patents, Technical Efficacy Thesaurus, Application Domain, Technology Topic, Popular Technical Reports.
© 2024 PatSnap. All rights reserved.Legal|Privacy policy|Modern Slavery Act Transparency Statement|Sitemap|About US| Contact US: help@patsnap.com