Hydraulic active control vibration absorbing support for railway emergency repair steel truss girder
A technology of active control and steel truss girders, which is applied in bridges, bridge parts, bridge construction, etc., can solve the problems of train running speed, vibration reduction, and impact on vehicle safety and stability that limit the application range of steel truss girders, so as to improve vehicle traffic The effect of speed and safety, reducing the displacement change of the beam structure, and improving the running stability
- Summary
- Abstract
- Description
- Claims
- Application Information
AI Technical Summary
Problems solved by technology
Method used
Image
Examples
Embodiment Construction
[0034] In order to make the purpose, technical solution and advantages of the present invention clearer, the invention will be clearly and completely described below in conjunction with the accompanying drawings and specific embodiments.
[0035] It is to be understood that the terms "central", "vertical", "transverse", "upper", "lower", "front", "rear", "left", "right", "vertical", "horizontal" ", "top", "bottom", "inner", "outer" and other indicated orientations or positional relationships are based on the orientations or positional relationships shown in the drawings, and are only for the convenience of describing the present invention and simplifying the description, rather than indicating Or imply that the device or element referred to must have a specific orientation, be constructed and operate in a specific orientation, and therefore should not be construed as limiting the invention.
[0036] Such as Figure 1-10 As shown, a hydraulic active control damping support for...
PUM
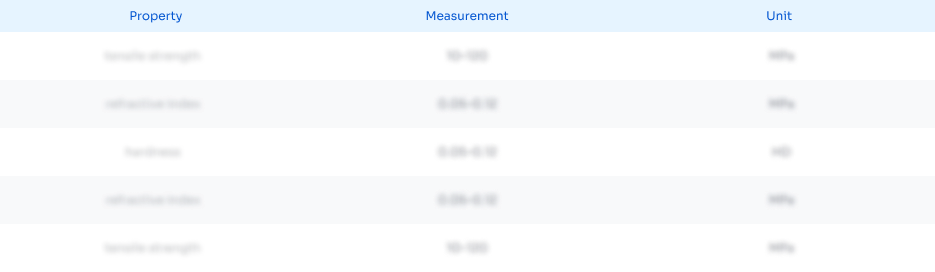
Abstract
Description
Claims
Application Information

- R&D
- Intellectual Property
- Life Sciences
- Materials
- Tech Scout
- Unparalleled Data Quality
- Higher Quality Content
- 60% Fewer Hallucinations
Browse by: Latest US Patents, China's latest patents, Technical Efficacy Thesaurus, Application Domain, Technology Topic, Popular Technical Reports.
© 2025 PatSnap. All rights reserved.Legal|Privacy policy|Modern Slavery Act Transparency Statement|Sitemap|About US| Contact US: help@patsnap.com