Silane crosslinked polyethylene cable insulation material
A silane crosslinking and cable insulation technology, applied in insulators, organic insulators, plastic/resin/wax insulators, etc., to achieve the effects of short crosslinking time, good mechanical properties and thermal aging resistance
- Summary
- Abstract
- Description
- Claims
- Application Information
AI Technical Summary
Problems solved by technology
Method used
Image
Examples
Embodiment 1
[0028] A silane cross-linked polyethylene cable insulation material is prepared by the following process:
[0029] (1) Put 60 parts of LLDPE7042 and 40 parts of LDPE (LD165) into the mixer by weight and stir at low speed for 1 minute and then at high speed for 3 minutes to obtain polyethylene raw materials;
[0030] (2) 30 parts of PVA1788 and 70 parts of PVA1799 were put into the mixer by weight and stirred at low speed for 1 minute and then stirred at high speed for 3 minutes to obtain polyvinyl alcohol raw material;
[0031] (3) 5 parts of polyethylene raw materials, 0.05 part of zirconium disulfide and 0.05 part of antioxidant 1024 are put into the blender by weight and stirred at low speed for 1 minute and then stirred at high speed for 3 minutes, then poured into the extruder hopper, extruded The exit temperature is 150°C. After being extruded by twin-screw, it is cooled in a cooling water tank, dried by a fan, and then pelletized, and then dried in a drying tower at 80°...
Embodiment 2
[0039] A silane cross-linked polyethylene cable insulation material is prepared by the following process:
[0040] (1) Put 80 parts of LLDPE7042 and 20 parts of LDPE (LD165) into a mixer by weight and stir at low speed for 1 minute and then at high speed for 3 minutes to obtain polyethylene raw materials;
[0041] (2) 70 parts of PVA1788 and 30 parts of PVA1799 were put into the blender by weight and stirred at low speed for 1 minute and then stirred at high speed for 3 minutes to obtain polyvinyl alcohol raw material;
[0042] (3) 10 parts of said polyethylene raw materials, 0.5 part of zirconium disulfide and 0.2 part of antioxidant 1024 are put into the blender in parts by weight and stirred at low speed for 1 minute and then stirred at high speed for 3 minutes, then poured into the extruder hopper, extruded The exit temperature is 150°C. After being extruded by twin-screw, it is cooled in a cooling water tank, dried by a fan, and then pelletized, and then dried in a drying...
Embodiment 3
[0050] A silane cross-linked polyethylene cable insulation material is prepared by the following process:
[0051] (1) Put 70 parts of LLDPE7042 and 30 parts of LDPE (LD165) into a mixer by weight and stir at low speed for 1 minute and then at high speed for 3 minutes to obtain polyethylene raw materials;
[0052] (2) Put 50 parts of PVA1788 and 50 parts of PVA1799 into a mixer by weight and stir at a low speed for 1 minute and then stir at a high speed for 3 minutes to obtain a polyvinyl alcohol raw material;
[0053] (3) 8 parts of polyethylene raw materials, 0.25 parts of zirconium disulfide and 0.1 part of antioxidant 1024 are put into the blender by weight and stirred at low speed for 1 minute and then stirred at high speed for 3 minutes, then poured into the extruder hopper, extruded The exit temperature is 150°C. After being extruded by twin-screw, it is cooled in a cooling water tank, dried by a fan, and then pelletized, and then dried in a drying tower at 80°C for 2 h...
PUM
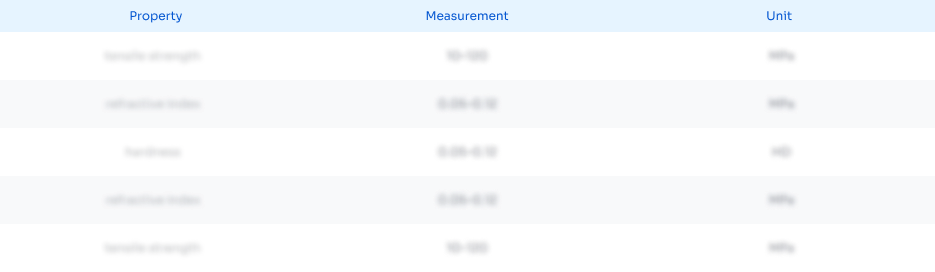
Abstract
Description
Claims
Application Information

- Generate Ideas
- Intellectual Property
- Life Sciences
- Materials
- Tech Scout
- Unparalleled Data Quality
- Higher Quality Content
- 60% Fewer Hallucinations
Browse by: Latest US Patents, China's latest patents, Technical Efficacy Thesaurus, Application Domain, Technology Topic, Popular Technical Reports.
© 2025 PatSnap. All rights reserved.Legal|Privacy policy|Modern Slavery Act Transparency Statement|Sitemap|About US| Contact US: help@patsnap.com