Automatic material stacking, material taking and material stacking and taking method and system for material yard
A material and material yard technology, applied in the field of 3D laser scanning, can solve the problems of energy consumption, loss, lack of safety, etc., and achieve the effect of reducing empty running, accurate movement direction, and improving operation accuracy.
- Summary
- Abstract
- Description
- Claims
- Application Information
AI Technical Summary
Problems solved by technology
Method used
Image
Examples
Embodiment 1
[0072] 1. The steps of the automatic stacking method for the material yard
[0073] Such as figure 1 as shown, figure 1 A schematic flow diagram of an automatic stacking method for a material field provided in the embodiment of the present invention; the automatic stacking method comprises the following steps:
[0074] Use the 3D laser scanner fixedly installed above the stock yard to scan the stock yard materials to form the first point cloud data of the materials;
[0075] Carrying out three-dimensional modeling of the material in the stockyard according to the first point cloud data and preset reference feature points to form a three-dimensional model of the stockyard;
[0076] According to the three-dimensional model of the stockyard, the alignment angle of the operation is obtained to complete the stacking operation;
[0077] Wherein, the three-dimensional modeling includes the following sub-steps:
[0078] Cleaning step: cleaning the first point cloud data to form se...
Embodiment 2
[0134] see Figure 4 , Figure 4 It is an automatic stacking system for a material yard provided by Embodiment 2. The automatic stacking system includes a three-dimensional laser scanner, a cleaning module, a splicing module, a removal module, a filling module, a modeling module, an angle alignment module and stacker;
[0135] Use the 3D laser scanner fixedly installed above the stockyard to scan the stockyard materials to form the first point cloud data;
[0136] The cleaning module is used to clean the first point cloud data to form second point cloud data;
[0137] The splicing module is used to splice the second point cloud data to obtain the third point cloud data;
[0138] The three-dimensional laser scanner acquires the point cloud data of the stacking arm on the blanking and stacking surface of the material, and the removal module is used to remove the point cloud data of the stacking arm from the third point cloud data to obtain the fourth point cloud data ;
[0...
Embodiment 3
[0144] 1. The steps of the automatic reclaiming method for the material yard
[0145] Such as Figure 5 as shown, Figure 5 A schematic flow diagram of an automatic retrieving method for a material field provided by Embodiment 3 of the present invention; the automatic retrieving method may include the following steps:
[0146] Use the 3D laser scanner fixedly installed above the stock yard to scan the stock yard materials to form the first point cloud data of the materials;
[0147] Carrying out three-dimensional modeling of the material in the stockyard according to the first point cloud data and preset reference feature points to form a three-dimensional model of the stockyard;
[0148] According to the three-dimensional model of the stockyard, the reclaimer obtains the starting point and the ending point of the operation, and completes the reclaiming operation based on the starting point and the ending point;
[0149] Wherein, the three-dimensional modeling includes the ...
PUM
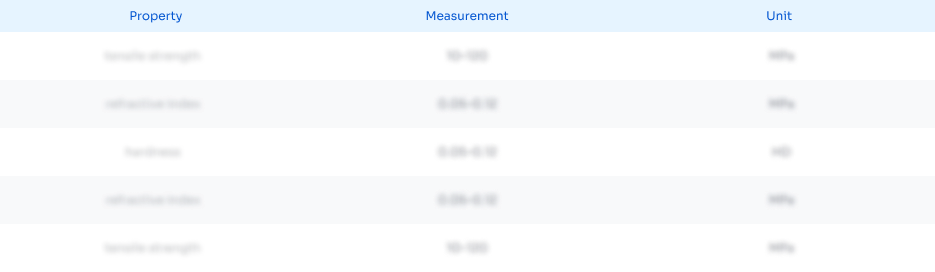
Abstract
Description
Claims
Application Information

- R&D
- Intellectual Property
- Life Sciences
- Materials
- Tech Scout
- Unparalleled Data Quality
- Higher Quality Content
- 60% Fewer Hallucinations
Browse by: Latest US Patents, China's latest patents, Technical Efficacy Thesaurus, Application Domain, Technology Topic, Popular Technical Reports.
© 2025 PatSnap. All rights reserved.Legal|Privacy policy|Modern Slavery Act Transparency Statement|Sitemap|About US| Contact US: help@patsnap.com