A method for energy-saving transformation of high-gradient magnetic separator for mineral processing
A high-gradient magnetic separator and magnetic separation technology, applied in high-gradient magnetic separators, chemical instruments and methods, magnetic separation, etc., can solve problems such as large power consumption, and achieve high energy consumption, cost reduction, and The effect of manufacturing costs
- Summary
- Abstract
- Description
- Claims
- Application Information
AI Technical Summary
Problems solved by technology
Method used
Image
Examples
Embodiment 1
[0040] Refer to the attached figure 2 , a modified energy-saving high-gradient magnetic separator for mineral processing, including a frame 1, a magnetic separation part 2, a magnetic system 3, a piping system and a collection part; the frame 1 includes a lower base 1-1 and an upper support frame 1 -2.
[0041] The magnetic separation part 2 is installed on the lower base 1-1, and the magnetic system 3 is fixedly installed on the outside of the magnetic separation part 2 through the upper support frame 1-2; the magnetic separation part 2 is an internal hollow cavity structure with a magnetic separation cavity wall 2-1, which is made of magnetically permeable or paramagnetic material, such as magnetically permeable stainless steel; a magnetic separation medium 2-2 is arranged in the magnetic separation cavity of the magnetic separation part 2, and the magnetic separation medium 2-2 is a tooth filled with intervals Plate media, space-packed rod media, tightly-packed spherical ...
Embodiment 2
[0055] A transformation method for transforming the electromagnetic coil type high gradient magnetic separator for mineral processing in the prior art into the energy-saving high gradient magnetic separator for mineral processing in Example 1, refer to the appendix. Figure 1-9 , the method is applied to electromagnetic coil type high gradient magnetic separator 0, which includes: upper pipeline 0-1, magnetic separation cavity 0-2, electromagnetic coil group 0-3, coil shell 0-4, support 0-5, Lower pipeline 0-6, cooling system 0-7; the method has the following modification steps:
[0056] (1) Power off the electromagnetic coil type high gradient magnetic separator 0, drain the slurry in the magnetic separation chamber 0-2, and drain the cooling liquid (such as oil or water) in the cooling system 0-7 and the coil shell 0-4. ) drain cleanly, disconnect the pipeline connected with the upper pipeline 0-1 and the lower pipeline 0-6;
[0057] (2) Remove the external related accessor...
Embodiment 3
[0065] see attached Figure 9 , a low-power energy-saving high-gradient magnetic separator for enhanced mineral processing, which adds a spiral pipe 3-1 and its matching collection tray 3-2, traction rope 3- 3. The lifting device 3-4 and the permanent magnet 3-5 use double-layer spiral pipes, the two spiral pipes have opposite directions of rotation, and the permanent magnets 3-5 in the two spiral pipes 3-1 attract the polarity sequence of the head and tail On the contrary, so that the magnetic system 3 can generate the magnetic field lines superimposed in the same direction in the magnetic separation cavity of the magnetic separation part 2 to improve the strength of the magnetic field formed in the magnetic separation cavity of the magnetic separation part 2, its working principle and control method The same as in Example 1.
PUM
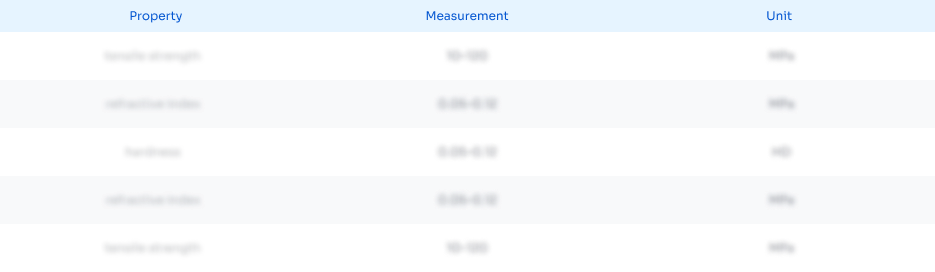
Abstract
Description
Claims
Application Information

- R&D
- Intellectual Property
- Life Sciences
- Materials
- Tech Scout
- Unparalleled Data Quality
- Higher Quality Content
- 60% Fewer Hallucinations
Browse by: Latest US Patents, China's latest patents, Technical Efficacy Thesaurus, Application Domain, Technology Topic, Popular Technical Reports.
© 2025 PatSnap. All rights reserved.Legal|Privacy policy|Modern Slavery Act Transparency Statement|Sitemap|About US| Contact US: help@patsnap.com