Injection components for die casting systems
A technology for injection components and pressure molds, applied in the field of injection components, which can solve problems such as machine downtime, deterioration of cooling systems, and damage to the quality of castings
- Summary
- Abstract
- Description
- Claims
- Application Information
AI Technical Summary
Problems solved by technology
Method used
Image
Examples
Embodiment Construction
[0017] DETAILED DESCRIPTION OF THE PREFERRED EMBODIMENTS With reference to the cited figures, an injection assembly according to the invention, indicated generally by reference numeral 1 , comprises an injection cylinder 19 suitable for injecting liquid metal into a mold 21 .
[0018] According to the invention, the oil pressure control circuit has only one control valve 22 which is inserted at the input between the accumulator 20 and the injection cylinder 19 and which controls the entire profile of the injection process.
[0019] The hydraulic fluid required to move the injection cylinder 19 is drawn from the accumulator 20 and introduced into the piston-side chamber 4 of the injection cylinder 19 by means of the control valve 22 and the non-return valve 2 .
[0020] The accumulator 20 contains hydraulic fluid at a given pressure.
[0021] The injection cylinder 19 is also provided with an annular chamber 5 which is connected to the accumulator 20 by means of the conduit 15 ...
PUM
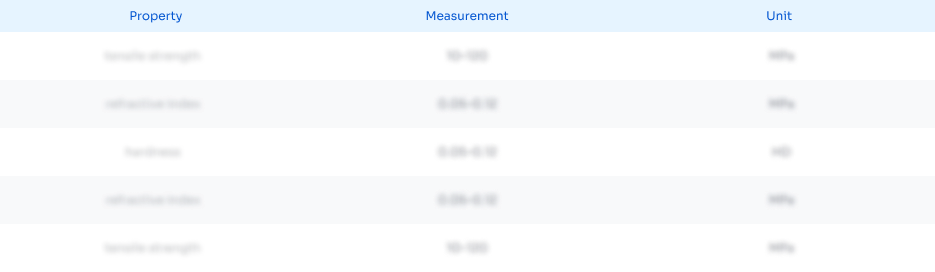
Abstract
Description
Claims
Application Information

- Generate Ideas
- Intellectual Property
- Life Sciences
- Materials
- Tech Scout
- Unparalleled Data Quality
- Higher Quality Content
- 60% Fewer Hallucinations
Browse by: Latest US Patents, China's latest patents, Technical Efficacy Thesaurus, Application Domain, Technology Topic, Popular Technical Reports.
© 2025 PatSnap. All rights reserved.Legal|Privacy policy|Modern Slavery Act Transparency Statement|Sitemap|About US| Contact US: help@patsnap.com